Plate Buckling Assessment According to LR CSR (2024) – Hand Calculations vs. SDC Verifier Validation
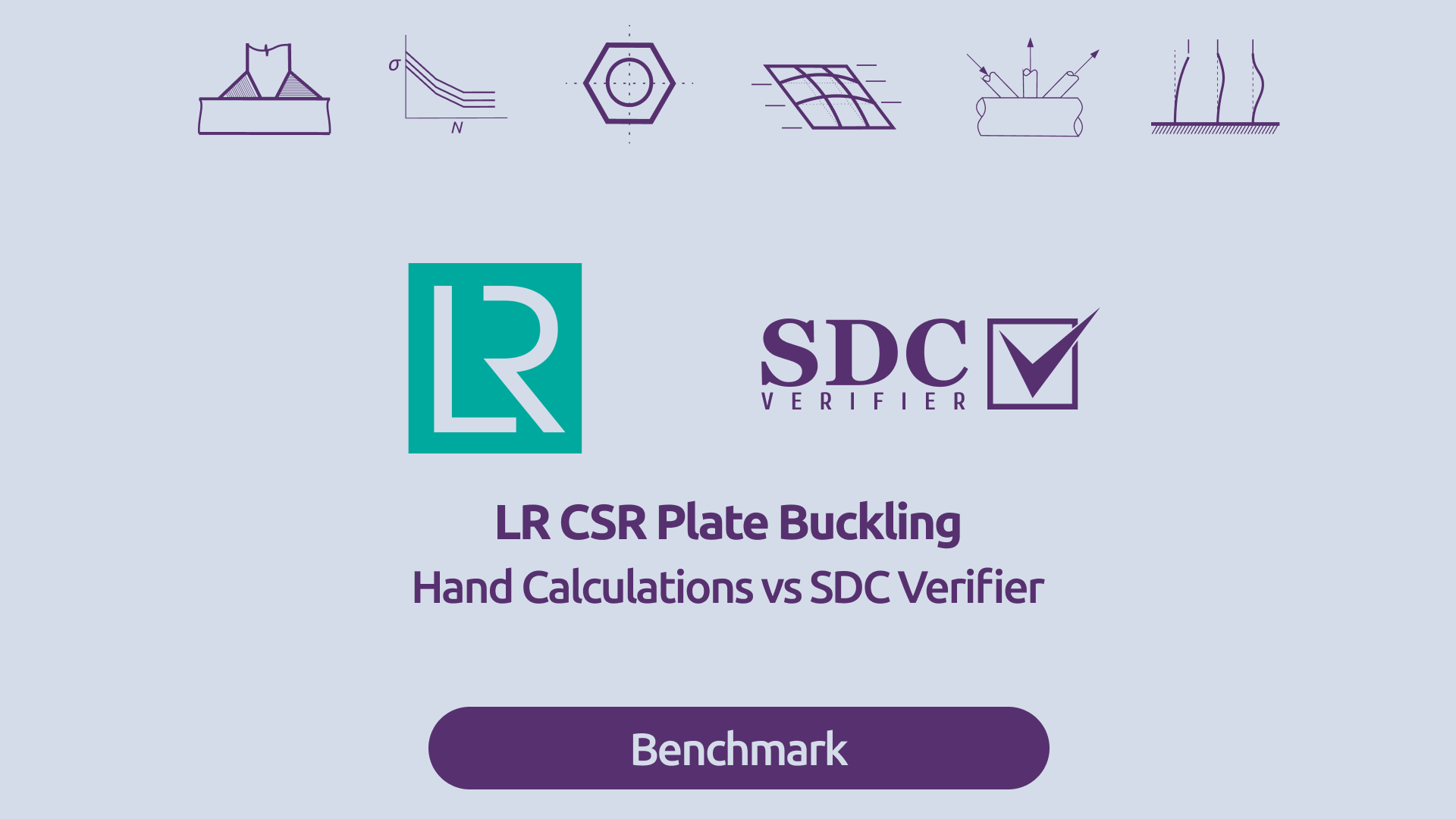
This benchmark evaluates the accuracy and reliability of plate buckling analysis performed using SDC Verifier by comparing it with detailed hand calculations based on the LR Common Structural Rules (CSR) for Bulk Carriers and Oil Tankers (2024 edition), specifically Part 1, Chapter 8 – Buckling.
A test plate with dimensions 10.2 × 5.4 × 1.1 meters was modeled and loaded with a combination of axial, transverse, and shear forces. One of the top plates—3.4 × 1.35 meters with 12 mm thickness—was selected for a focused verification check. The material used was mild steel, and all boundary conditions, loading scenarios, and code-based coefficients were applied consistently across both calculation methods.
The objective was to:
-
Verify slenderness requirements,
-
Calculate elastic buckling stress and critical stress factors,
-
Solve all four LR CSR limit state equations analytically,
-
Derive ultimate buckling stresses and utilization factor,
-
Validate results via a full FEM simulation and SDC Verifier check.
A test plate model with 10.2 × 5.4 × 1.1 m dimensions was designed for the purpose of this benchmark:
The model was constrained at four bottom corners where side plates are connected. Forces were applied on the edges of the top plate with the following values:
-
∣FL+∣=∣FL−∣=3000 kN|F_L^+| = |F_L^-| = 3000 text{kN}
-
∣FS+∣=∣FS−∣=2550 kN|F_S^+| = |F_S^-| = 2550 text{kN}
-
∣FP+∣=∣FP−∣=2500 kN|F_P^+| = |F_P^-| = 2500 text{kN}
Selected Plate and Material Properties
One of the top plates was chosen for all the calculations included in the check.
Plate dimensions:
-
Length: a=3.400 ma = 3.400 m
-
Width: b=1.350 mb = 1.350 m
-
Thickness: tp=0.012 mt_p = 0.012 m
Mild steel material properties:
-
Young’s Modulus: E=210 GPaE = 210 GPa
-
Poisson’s Ratio: ν=0.3nu = 0.3
-
Mass Density: ρ=7850 kg/m3rho = 7850 kg/m^3
-
Tensile Strength: Rm=360 MPaR_m = 360 MPa
-
Yield Stress: ReH,P=235 MPaR_{eH,P} = 235 MPa
Due to the complexity of the model, all required stress values were obtained with the help of FEM.
Obtained values:
-
σx=37.14 MPasigma_x = 37.14 MPa
-
σy=25.12 MPasigma_y = 25.12 MPa
-
τ=16.34 MPatau = 16.34 MPa
In order to check the results, analytical calculations were first carried out.
Slenderness requirement check (Pt. 1, Ch. 8, Sec. 2 / [2.2.1]):
tp>bcReH235t_p > frac{b}{c} sqrt{frac{R_{eH}}{235}}
12 mm>1350125⋅235235 mm
✅ 12 mm > 10.8 mm
Final Equations for Limit States
(According to code Pt. 1, Ch. 8, Sec. 5 / [2.2.1]):
I.
(γc1σxSσcx′)e0−B(γc1σxSσcx′)e02(γc1σySσcy′)e02+(γc1σySσcy′)e0+(γc1∣τ∣Sτc′)e0=1
II. (when σx≥0sigma_x geq 0)
(γc2σxSσcx′)2βp0.25+(γc2∣τ∣Sτc′)2βp0.25=1
III. (when σy≥0sigma_y geq 0)
(γc3σySσcy′)2βp0.25+(γc3∣τ∣Sτc′)2βp0.25=1
IV.
γc4∣τ∣Sτc′=1
Aspect Ratio of the Plate Panel
(Pt. 1, Ch. 8, Sec. 5 / Symbols)
The aspect ratio αalpha of the plate panel is defined as the ratio of its length aa to width bb:
α=abα=3.401.35α=2.519
Elastic Buckling Reference Stress
(Pt. 1, Ch. 8, Sec. 5 / Symbols)
The elastic buckling reference stress σEsigma_E was calculated using the formula:
σE=π2E12(1−ν2)(tpb)2
Substituting the known values:
σE=π2⋅210⋅10912⋅(1−0.32)(0.0121.35)2 Pasigma_E = frac{pi^2 cdot 210 cdot 10^9}{12 cdot (1 – 0.3^2)} left(frac{0.012}{1.35}right)^2 text{Pa}
σE=14 996 549.9 Pa
Edge Stress Ratio and Correction Factors
-
Edge stress ratio ψpsi was set as 1 in both directions:
ψ=1
(Pt. 1, Ch. 8, Sec. 5 / Symbols; stresses calculated using weighted average approach, Pt. 1, Ch. 8, App. 1 / [2.2.1]) -
Correction factor FlongF_{long} was set as 1:
Flong=1
(Pt. 1, Ch. 8, Sec. 5 / [2.2.4]; Table 2) -
Correction factor FtranF_{tran} was also set as 1:
Ftran=1
(Pt. 1, Ch. 8, Sec. 5 / [2.2.5])
Ultimate buckling stresses were calculated in 3 cases:
(Pt. 1, Ch. 8, Sec. 5 / Table 3)
Case 1:
Plate Buckling Setup
The plate is compressed along the x-direction with an edge stress ratio ψ=1psi = 1.
Intermediate Parameters:
-
Effective width factor
c=min((1.25−0.12ψ), 1.25)=min(1.13, 1.25)=1.13c = min left( (1.25 – 0.12psi), 1.25 right) = min(1.13, 1.25) = 1.13 -
Slenderness parameter
λc=c2(1+1−0.88c)=1.132(1+1−0.881.13)=0.831lambda_c = frac{c}{2} left( 1 + sqrt{1 – frac{0.88}{c}} right) = frac{1.13}{2} left( 1 + sqrt{1 – frac{0.88}{1.13}} right) = 0.831 -
Buckling coefficient in x-direction
Kx=Flong⋅8.4ψ+1.1=1⋅8.41+1.1=4
Reference Degree of Slenderness in x-direction
(Pt. 1, Ch. 8, Sec. 5 / [2.2.2])
λx=ReH,PKx⋅σE
Substituting values:
λx=235×1064×14996549.9=1.979
Reduction Factor for Stress in x-direction CxC_x
(Pt. 1, Ch. 8, Sec. 5 / Table 3)
Cx=c(1λx−0.22λx2)C_x = c left( frac{1}{lambda_x} – frac{0.22}{lambda_x^2} right)
Cx=1.13×(11.979−0.221.9792)=0.507
Case 2:
Parameters:
c=min((1.25−0.12ψ),1.25)=min((1.25−0.12⋅1),1.25)=1.13c = min((1.25 – 0.12psi), 1.25) = min((1.25 – 0.12 cdot 1), 1.25) = 1.13
λc=c2(1+1−0.88c)=1.132(1+1−0.881.13)=0.831lambda_c = frac{c}{2} left( 1 + sqrt{1 – frac{0.88}{c}} right) = frac{1.13}{2} left( 1 + sqrt{1 – frac{0.88}{1.13}} right) = 0.831
f1=(1−ψ)(α−1)=(1−1)(2.519−1)=0f_1 = (1 – psi)(alpha – 1) = (1 – 1)(2.519 – 1) = 0
Ky=Ftran⋅2(1+1α2)21+ψ+1−ψ100⋅(2.4⋅α2+6.9⋅f1)K_y = F_{tran} cdot frac{2 left( 1 + frac{1}{alpha^2} right)^2}{1 + psi + frac{1 – psi}{100} cdot (2.4 cdot alpha^2 + 6.9 cdot f_1)}
Ky=1⋅2(1+12.5192)21+1+1−1100⋅(2.4⋅2.5192+6.9⋅0)=1.340
Reference Degree of Slenderness in Y Direction λᵧ
(Pt. 1, Ch. 8, Sec. 5 / [2.2.2])
λy=ReH,PKy⋅σElambda_y = sqrt{ frac{R_{eH,P}}{K_y cdot sigma_E} }
λy=235⋅1061.340⋅14996549.9=3.419lambda_y = sqrt{ frac{235 cdot 10^6}{1.340 cdot 14996549.9} } = 3.419
Factor c1c_1
(Pt. 1, Ch. 8, Sec. 5 / [2.2.3])
The coefficient c1c_1 was calculated using the SP-A assessment method:
c1=(1−1α),and c1≥0
Substituting:
c1=(1−12.519)=0.603
R=0.220R = 0.220
λp2=λy2−0.5and1≤λp2≤3lambda_p^2 = lambda_y^2 – 0.5 quad text{and} quad 1 leq lambda_p^2 leq 3
λp2=3.4192−0.5=3(satisfies range)
Calculation of FF
F=(1−(Ky0.91−1)1λp2)⋅c1,F≥0F = left( 1 – left( frac{K_y}{0.91} – 1 right) frac{1}{lambda_p^2} right) cdot c_1, quad F geq 0F=(1−(1.3400.91−1)⋅13)⋅0.603=0.508
Calculation of TT
T=λy+1415λy+13T = lambda_y + frac{14}{15lambda_y} + frac{1}{3}
T=3.419+1415⋅3.419+13=4.026T = 3.419 + frac{14}{15 cdot 3.419} + frac{1}{3} = 4.026
Calculation of HH
H=λy−2λyc(T+T2−4),H≥RH = lambda_y – frac{2lambda_y}{c(T + sqrt{T^2 – 4})}, quad H geq R
H=3.419−2⋅3.4191.13⋅(4.026+4.0262−4)=2.614(valid since H>R=0.22)
Reduction Factor for Stress in Y Direction CyC_y
(Pt. 1, Ch. 8, Sec. 5 / Table 3)
Cy=c(1λy−R+F2(H−R)λy2)
Substituted values:
Cy=1.13⋅(13.419−0.22+0.5082⋅(2.614−0.22)3.4192)C_y = 1.13 cdot left( frac{1}{3.419} – frac{0.22 + 0.508^2 cdot (2.614 – 0.22)}{3.419^2} right)
Cy=0.250
Case 15:
Kτ=3(5.34+4α2)
Substituted values:
Kτ=3(5.34+42.5192)K_tau = sqrt{3} left( 5.34 + frac{4}{2.519^2} right)
Kτ=10.341
Reference degree of slenderness in xyxy direction λτlambda_tau
(Pt. 1, Ch. 8, Sec. 5 / [2.2.2])
λτ=ReH,PKτ⋅σE
Substituted values:
λτ=235×10610.341×14996549.9=1.231
Reduction factor for stress in xyxy direction CτC_tau
(Pt. 1, Ch. 8, Sec. 5 / Table 3)
Cτ=0.84λτ
Substituted values:
Cτ=0.841.231=0.682
Ultimate buckling stresses
(Pt. 1, Ch. 8, Sec. 5 / [2.2.3])
In the direction parallel to the longer edge of the buckling panel:
σcx′=CxReH,Psigma’_{cx} = C_x R_{eH,P}
σcx′=0.507⋅235 MPa=119.145 MPa
In the direction parallel to the shorter edge of the buckling panel:
σcy′=CyReH,Psigma’_{cy} = C_y R_{eH,P}
σcy′=0.250⋅235 MPa=58.750 MPa
Shear:
τc′=Cτ⋅ReH,P3tau’_c = C_tau cdot frac{R_{eH,P}}{sqrt{3}}
τc′=0.682⋅235 MPa3=92.532 MPa
The rest of the input parameters for final equations were calculated:
Plate slenderness parameter
(Pt. 1, Ch. 8, Sec. 5 / [2.2.1]):
βp=btpReH,PEbeta_p = frac{b}{t_p} sqrt{frac{R_{eH,P}}{E}}
βp=1.3500.012⋅235⋅106210⋅109=3.763
Coefficient BB
(Pt. 1, Ch. 8, Sec. 5 / Table 1):
B=0.7−0.3⋅βpα2B = 0.7 – frac{0.3 cdot beta_p}{alpha^2}
B=0.7−0.3⋅3.7632.5192=0.522
Coefficient e0e_0
(Pt. 1, Ch. 8, Sec. 5 / Table 1):
e0=2βp0.25e_0 = frac{2}{beta_p^{0.25}}
e0=23.7630.25=1.436
Final Equations for Limit States
(Pt. 1, Ch. 8, Sec. 5 / [2.2.1]) — Transformed to calculate stress multiplier factors acting on loads γgamma
I.
γc1=(1(σxSσcx′)e0−B(σxSσcx′)e02(σySσcy′)e02+(σySσcy′)e0+(∣τ∣Sτc′)e0)1e0
II.
γc2=(1(σxSσcx′)2βp0.25+(∣τ∣Sτc′)2βp0.25)βp0.252
III.
γc3=(1(σySσcy′)2βp0.25+(∣τ∣Sτc′)2βp0.25)βp0.252
IV.
γc4=τc′∣τ∣S
Partial Safety Factor and Stress Multiplier Factors
The partial safety factor SS (Pt. 1, Ch. 8, Sec. 5 / Symbols) was set as:
S=1S = 1
Then the values of stress multiplier factors acting on loads γgamma were calculated:
I.
γc1=1.763
II.
γc2=2.486
III.
γc3=1.968
IV.
γc4=5.663
Minimum Stress Multiplier Factor and Utilization Factor
The minimum stress multiplier factor from above – the stress multiplier factor at failure γcgamma_c – was found:
γc=1.763
The utilization factor ηacteta_{act} was calculated (Pt. 1, Ch. 8, Sec. 1 / [3.2.2]):
ηact=1γc=11.763=0.567
SDC Verifier Setup
In SDC Verifier, the standard was added using the same assumptions as in the analytical calculation. The check was then performed based on this setup.
1. Mild Steel Properties
Top Plate Properties (T = 12 mm)
Properties Summary
Calculated for the CSys “0..Basic Rectangular”
FEM Loads
This paragraph contains information about applied loads to model.
1. Long edges
2. Short edges
3. Long edges parallel
Constraints
This paragraph contains information about constrained parts of the model.
Results
1..Job 1
Load Sets
In this paragraph, the influence of the different load combinations is described.
Load Set ‘1..Load Set 1’
3..LR CSR Plate Buckling (2024)
Standard implemented according to
LR Common Structural Rules for Bulk Carriers and Oil Tankers, January 2024
based on the following part of the standard
Part 1, Chapter 8 – Buckling
Unit System
Current Unit System = MKS (Meter/Kg/Second). It is used in calculations for the following standards:
API RP 2A, ISO 19902, Norsok N004, DIN 15018, FEM 1.001 and Eurocode3.
Intermediate Results of σ′cx, σ′cy and τ′c from Calculation Details of the Check
Comparison of Hand Calculations and SDC Verifier Results
Parameter | Hand Calculations | SDC Verifier |
---|---|---|
Slenderness Requirement | ||
Passed | Passed |
Ultimate Buckling Stresses [MPa]
Parameter | Hand Calculations | SDC Verifier |
---|---|---|
σ′cx | 119.145 | 119.252 |
σ′cy | 58.750 | 58.631 |
τ′c | 92.932 | 92.585 |
Inverse of Stress Multiplier Factors Acting on Loads
Parameter | Hand Calculations | SDC Verifier |
---|---|---|
1/γc1 | 0.567 | 0.562 |
1/γc2 | 0.402 | 0.396 |
1/γc3 | 0.508 | 0.504 |
1/γc4 | 0.177 | 0.169 |
Utilization Factor
Parameter | Hand Calculations | SDC Verifier |
---|---|---|
ηact = 1 / γc1 | 0.567 | 0.562 |
Note: Results from SDC Verifier are the same as those obtained with hand calculations.
Conclusion
The benchmark confirms a high level of agreement between hand calculations and the automated SDC Verifier check:
-
The slenderness requirement was satisfied.
-
Differences in ultimate buckling stresses and stress multiplier factors were within <0.2%, indicating precise consistency.
-
The utilization factor obtained was nearly identical:
→ Hand calculations: ηact = 0.567
→ SDC Verifier: ηact = 0.562
This validation demonstrates that SDC Verifier accurately implements the LR CSR 2024 buckling assessment procedures, making it a dependable tool for structural integrity checks in maritime and offshore applications.