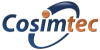
Achieving ABS Approval for a Shallow Draft Drilling System (SDDS) in Record Time
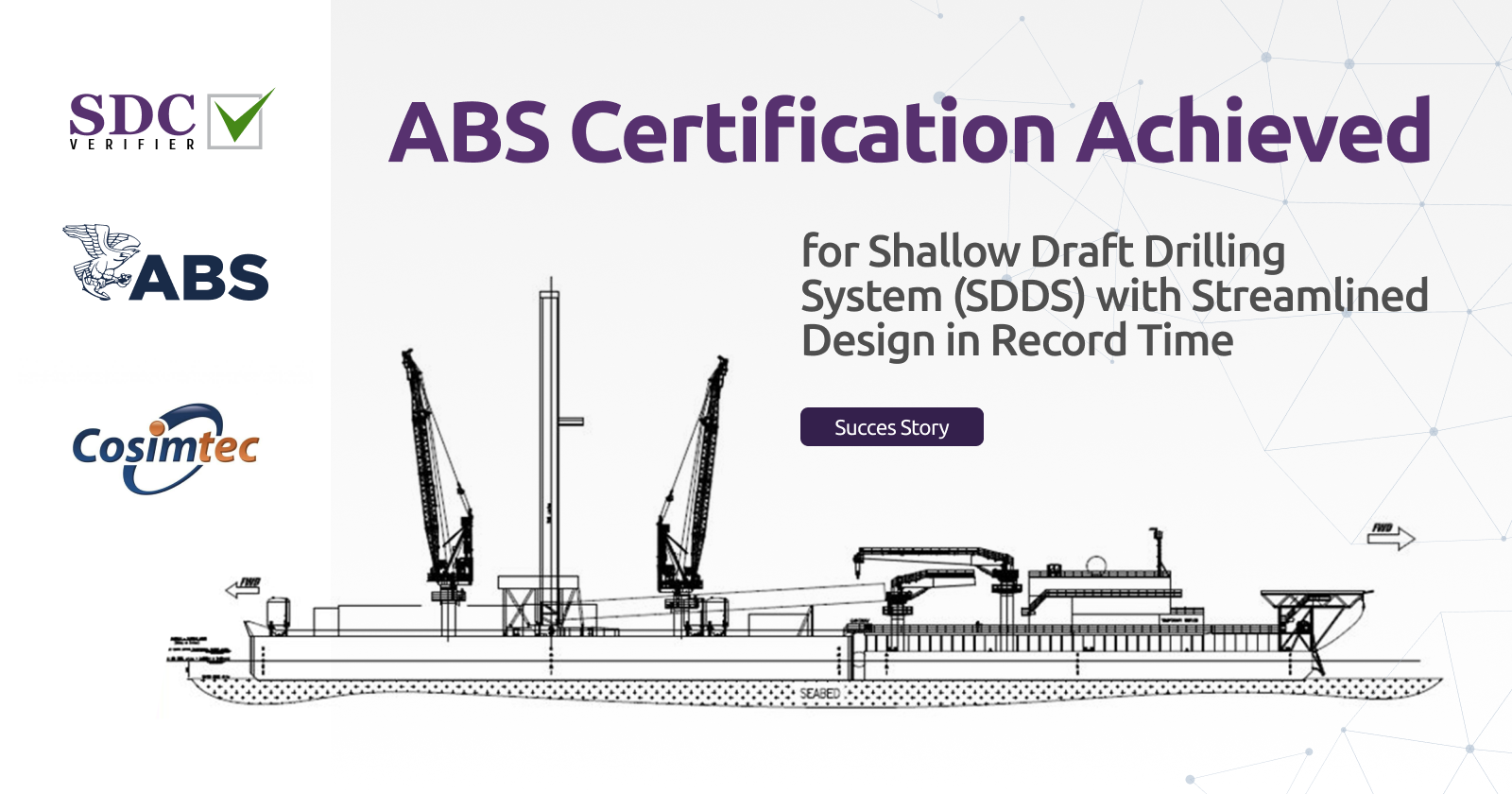
70%
Time saved on report generation
60%
Faster buckling checks
30%
Reduction in total project time
- The project applies FEA and code checks to validate the structural design of the Shallow Draft Drilling System (SDDS) for extreme shallow-water and wind conditions.
- Automated tools in SDC Verifier streamlined load application, buckling checks, and ABS compliance reporting, significantly reducing manual effort.
- Results enabled fast ABS approval with minimal comments, improving accuracy, reducing risks, and cutting overall project time by up to 30%.
The Shallow Draft Drilling System (SDDS) was developed to address a unique engineering challenge: designing a barge system capable of operating in less than 2-meter water depths in the North Caspian Sea, under restricted service conditions of up to 70-knot winds. This demanding environment required a design that balanced structural integrity with environmental adaptability.
Cosimtec Pte Ltd spearheaded the project, leveraging advanced engineering tools like Femap Simcenter Nastran for modeling and SDC Verifier for load applications, code checks, and report generation. By implementing automated workflows and minimizing inefficiencies, the team achieved ABS certification with minimal comments, safeguarding the project timeline and reducing financial risks.
Client Objective
The SDDS project aimed to design a barge system capable of safe and efficient drilling operations in less than 2 meters of water — a technical requirement that inherently restricted design options while amplifying operational risks. This system needed to perform reliably in shallow water environments while withstanding external stresses such as 70-knot winds, ensuring safety and structural integrity.
Meeting ABS standards for Mobile Offshore Units (MOUs) and Steel Barges was a critical requirement.
Furthermore, the client required a streamlined approval process to avoid costly delays. Prolonged review cycles and multiple iterations often incur significant resource and time expenditures. The team’s objective was to secure ABS certification efficiently, with minimal feedback, to enable a seamless transition to construction and deployment.
Shallow Draft Drilling System (SDDS) designed for drilling in water depths under 2 meters, approved by ABS for compliance with Mobile Offshore Unit standards and restricted service under 70-knot wind conditions.
Challenges
The SDDS project encountered a series of complex engineering challenges:
Managing Complex Loading Conditions
The structural model needed to account for dynamic forces, including buoyancy, tank loads, and environmental stresses. With 8 load cases, including Forces, Moments, Pressure, Buoyancy Load, and Tank Loads, the analysis had to cover a wide range of scenarios to ensure the design’s robustness. The finite element model itself was highly complex, comprising over 650,000 elements.
Additionally, ensuring a fully connected mesh model posed a challenge, which was successfully addressed using SDC Verifier’s Free Edge Tool. This feature greatly reduced the effort involved in verifying the mesh, ensuring a reliable and accurate analysis.
Stress distribution and deformation analysis for SDDS under sagging and hogging conditions. Elemental contour plots visualize Von Mises stresses and beam combined stresses, providing critical insights into structural performance under operational loads. (1- without Beam results; 2 – with Von Mises stresses; 3 – Von Mises stresses and beam combined stresses)
Regulatory Compliance Across Standards
The design had to adhere to the ABS Rules for Mobile Offshore Units and Steel Barges, alongside IMO Resolution A.1023 (26) for offshore drilling units. Each standard imposed detailed and overlapping criteria, demanding rigorous analytical workflows and meticulous documentation to withstand classification review.
Streamlining Labor-Intensive Processes
Tasks such as buckling checks and report generation were historically time-consuming, requiring significant manual input. Without optimization, these bottlenecks could have slowed down the approval cycle. Using SDC Verifier’s automated workflows, these processes were significantly streamlined, with time savings exceeding 60% for code checks and 70% for report generation.
Solutions
A comprehensive solution was implemented to address these challenges by integrating advanced engineering tools and automation.
Structural FEA Strength Calculation
Using Femap Simcenter Nastran, the team developed a detailed finite element model to simulate stress distributions and deformations accurately. SDC Verifier was employed for automated code checks, focusing on ABS OS standards for plate buckling.
While the IMO guidelines provided general recommendations on evaluating buckling strength, the ABS implementation within SDC Verifier ensured precise compliance with applicable criteria, streamlining the validation process and eliminating redundancies.
Finite Element Model (FEM) illustrating the SDDS structure under sagging conditions with support-floating. The visualization highlights load distribution and applied load cases, essential for structural validation.
Efficient Load Applications
SDC Verifier’s capabilities simplified the handling of buoyancy and tank loads, drastically reducing the manual effort typically required. Automated load creation saved more than 50% of the time typically spent on these tasks, allowing the team to iterate quickly and improve accuracy.
Visualization of load application and pressure distribution analysis in SDC Verifier. The central image highlights elemental pressure contours, demonstrating the system’s ability to model and validate complex load scenarios efficiently.
Buckling Checks
SDC Verifier replaced traditional spreadsheet-based calculations with integrated automated checks. This innovation accelerated the process while ensuring compliance with ABS Plate Buckling rules, freeing engineers to focus on design optimization. Time savings for buckling checks exceeded 60%.
Buckling state limit analysis for six plate groups using SDC Verifier. The contour plot illustrates utilization ratios with respect to the buckling limit state, while the tabulated data highlights key parameters such as ultimate strength and equivalent stress values, ensuring compliance with ABS Plate Buckling standards
Streamlined Report Generation
The automation of report generation within SDC Verifier enabled the production of comprehensive documentation tailored to ABS requirements. This transparency and clarity facilitated efficient regulatory review and expedited approvals. Time savings for report generation exceeded 70%.
Comprehensive model detail generation in SDC Verifier. This example highlights a 12 mm deck plate, showcasing material properties, element mass, and thickness distribution, all documented efficiently for rapid approval processes.
Results
The project achieved outstanding technical and operational results:
- Time Savings: Overall project time was reduced by 20-30%, with specific time savings of 10% for meshing, over 50% for load creation, 60% for code checks, and 70% for report generation.
- Accuracy and Compliance: Automated tools eliminated variability and ensured full compliance with ABS standard.
- Approval Without Delays: The comprehensive reports allowed ABS to review and approve the design with minimal comments, avoiding costly delays.
Conclusion
The SDDS project highlights the transformative power of modern engineering tools in overcoming complex challenges and meeting tight deadlines. By integrating structural design and analysis software SDC Verifier into the workflow, the team achieved precise structural validation, efficient handling of complex loads, and expedited reporting. This approach not only ensured compliance but also delivered substantial time and cost savings, proving the value of automation in compliance-driven engineering projects.