Static calculation of a cable winch
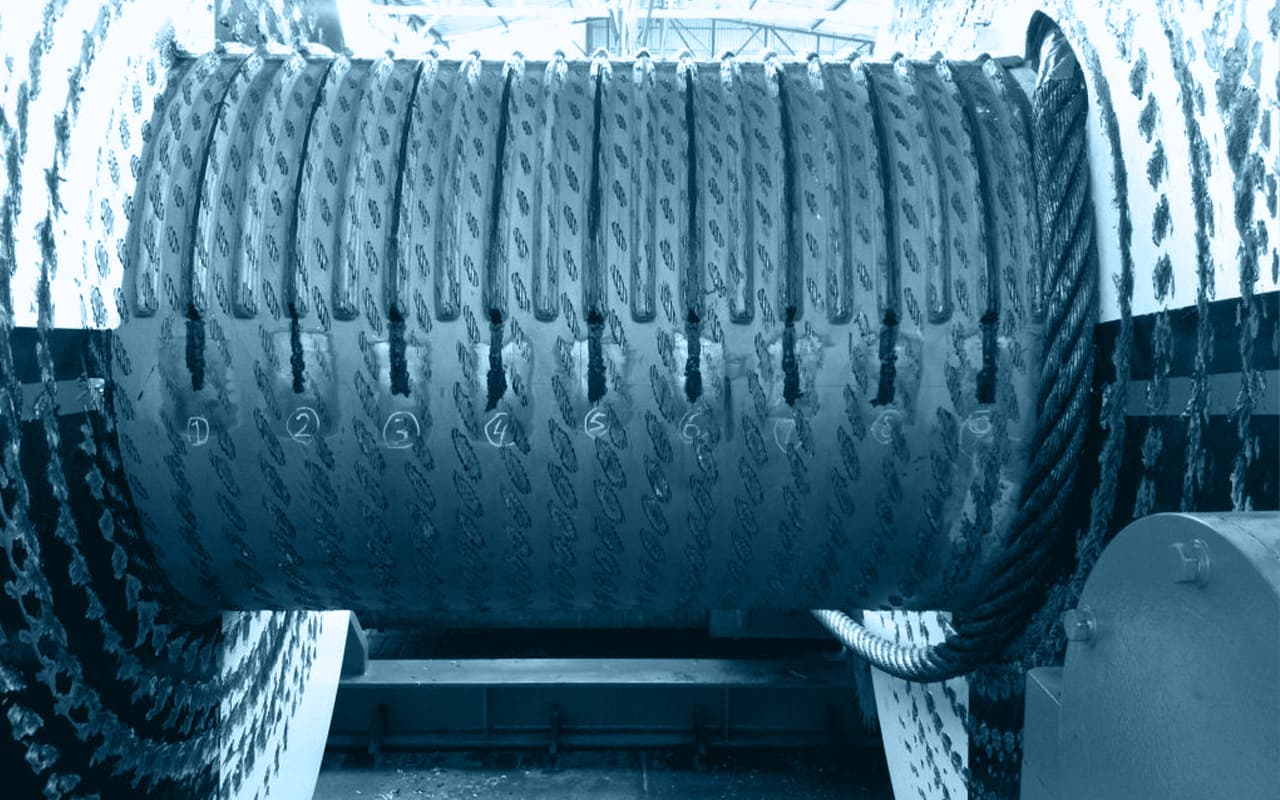
The design of a drum of a multilayer cable winch depends heavily on the maximum hoop pressure from the cable package. The DNV Rules for Certification of Lifting Appliances prescribes the hoop stress with a c-factor times the hoop pressure for single layer winches. In a 2008 revision, this factor was changed suddenly from 1.75 to 3 for 5 layers or more. This much higher c-value was justified because of a sudden drum failure of a multilayer hoisting winch. Although this is a good conservative approach for hoisting winches which have maximum tension forces over all layers, for mooring winches this results in the excessive barrel a flange thicknesses. For design and approval of a mooring winches with more reasonable plate thicknesses, a parametric FEA model was built to predict the compression stresses from the cable layers on the drum.
This model predicted that indeed for hoisting winches (=maximum tension forces over all layers in the drum) a c-value of 3 or higher, but for mooring winches with only a limited cable range with maximum tension forces c-values below 1.75 can be found. For verification of the FEM model and for the approval of the first winch design, full scale strain gauche tests have been carried out on a 270 mTon 11 layer anchor winch with 1250 m rope.
The results of the FEM model and the strain gauge tests are in good agreement and the lower effective c-value and the design are accepted for use as mooring winch (see the paper from OIPEEC conference 2013). For further verification of the model, the outcome is also compared with tests performed by prof. Dietz. The prediction of the new FEM-model is much closer to the measured values then if curves according to the pressure model of Dietz are used. (see paper from OIPEEC conference 2015) Besides a better accuracy compared to the Dietz method, the FEM model approach also allows studying the influence of all kinds of complex winch designs including for example effects of local stiffeners, stiffened flanges, and welding details.