Fatigue Strength and Limit: Understanding Materials-Specific Data
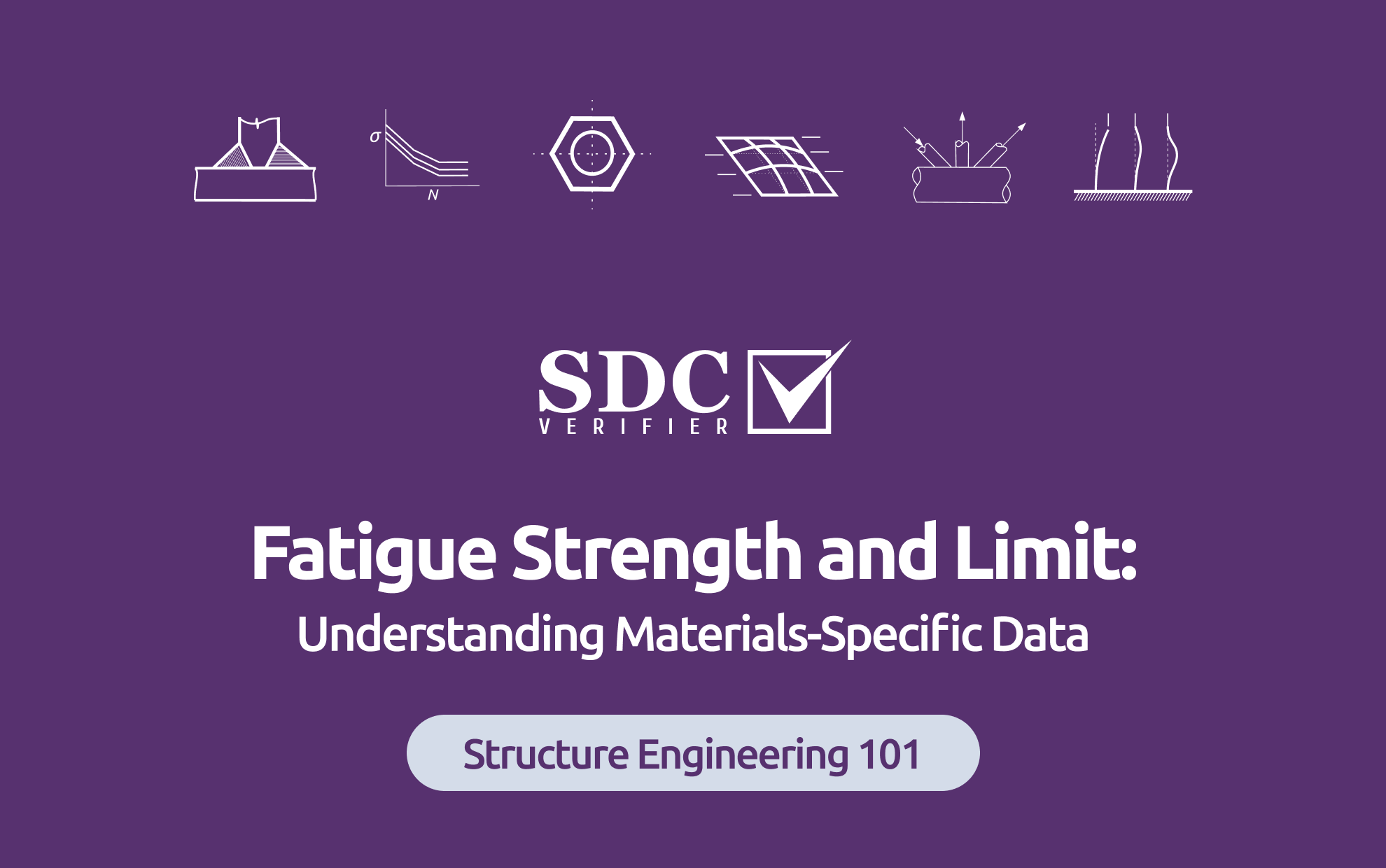
If you are worried about fatigue, knowing the difference between fatigue strength and fatigue limits can help in your issue. Fatigue strength is the maximum load a material can withstand for a given number of cycles before failing. The fatigue limit is the stress level below which the material can theoretically withstand an infinite number of cycles.
Different materials have unique fatigue behaviors influenced by factors like alloy composition and environmental conditions. So, considering material-specific data helps predict performance and ensures reliability and longevity in engineering applications.
To gain a deeper understanding of fatigue failure mechanisms and how engineers predict the fatigue life of components, watch this informative video:
Now that you understand the basics of fatigue failure, let’s explore the difference between fatigue strength and fatigue limit in more detail.
Fatigue Strength vs. Fatigue Limit
Though these terms are sometimes mistakenly used interchangeably, they represent distinct aspects of a material’s behavior under repeated stress.
Fatigue Strength
Fatigue strength is the maximum stress a material can endure for a specified number of cycles before failure occurs. For instance, a material might have a fatigue strength of 200 MPa for 10^6 cycles. This means that if the material is subjected to a cyclic stress of 200 MPa, there is a high probability of failure occurring after 10^6 cycles.
Such a conclusion follows this formula: σ′f=f(σm/σu). Fatigue strength assists in engineering design. It helps predict the lifespan of a component under repeated loading conditions. So, by knowing the fatigue strength, engineers can design components that avoid premature failure.
Fatigue Limit (Endurance Limit)
The fatigue limit, also known as the endurance limit, is the stress level below which a material can theoretically endure an infinite number of cycles without failing. This concept is especially relevant for materials like steel and titanium, which exhibit a distinct fatigue limit.
For example, if a steel alloy has a fatigue limit of 150 MPa, it means that the material can theoretically withstand cyclic stresses of up to 150 MPa indefinitely without experiencing fatigue failure. Therefore, not all materials have a defined fatigue limit. Non-ferrous metals like aluminum often do not exhibit a clear endurance limit.
Factors Influencing Fatigue Strength and Limits
Fatigue strength and limits are not set in stone; they are significantly influenced by a combination of factors. They involve the material’s inherent properties (such as its composition, microstructure, and heat treatment), the surrounding environmental conditions (like temperature, humidity, and corrosive agents), and the surface conditions of the component (such as roughness, residual stresses, and the presence of defects).
To visualize how cyclic loading can lead to fatigue cracking at the microscopic level, watch this video of a constant amplitude fatigue test:
Material Properties
A material’s fatigue resistance is inherently linked to its underlying properties, particularly its alloy composition and microstructure.
For instance, adding chromium and molybdenum to steel can significantly enhance its fatigue strength. On the contrary, elements like sulfur and phosphorus can act as detrimental impurities, promoting crack initiation and propagation.
High-strength steels, due to their fine-grained microstructure and controlled impurity levels, generally exhibit improved fatigue strength compared to lower strength grades. Also, heat treatments like quenching and tempering, and mechanical processes like forging and rolling, can greatly alter a material’s microstructure, directly influencing its fatigue performance.
You should carefully consider these material-specific characteristics when selecting materials for applications subjected to cyclic loading, as choosing the wrong material can lead to premature fatigue failure and costly consequences.
Environmental Factors
Environmental factors exert a powerful influence on a material’s fatigue resistance, with temperature and corrosion being key culprits.
Elevated temperatures can soften materials, which decreases their fatigue strength, while low temperatures may increase brittleness. It makes materials more susceptible to fatigue cracks.
Corrosive environments, such as saltwater or acidic substances, can accelerate fatigue failure through a process known as corrosion fatigue, where the combined action of cyclic stress and chemical attack weakens the material. It’s important to note that these environmental factors often act synergistically, meaning their combined effect can be more detrimental than the sum of their individual effects.
Surface Conditions
Rough surfaces, with their inherent notches and imperfections, act as stress concentrators, amplifying the local stress levels far beyond the nominal applied stress.
These localized high stresses create ideal conditions for the initiation of fatigue cracks, reducing the material’s fatigue life. Smoother surfaces, on the other hand, generally exhibit higher fatigue strength due to the reduced likelihood of crack initiation.
Surface treatments can further enhance fatigue resistance.
- Shot peening, for instance, introduces compressive residual stresses that counteract the tensile stresses experienced during cyclic loading, effectively hindering crack growth.
- Coatings, such as nitriding or carburizing, can create a harder and more wear-resistant surface layer, further improving fatigue performance.
Material-Specific Fatigue Data
Fatigue behavior of different materials is crucial for engineering applications. Here, we look at the fatigue properties of four common engineering materials: steel, aluminum, stainless steel, and titanium.
To understand the fatigue behavior of different materials, engineers utilize S-N curves (stress vs. number of cycles to failure). These curves visually represent the relationship between the cyclic stress amplitude a material can endure and the number of cycles it can withstand before failing. The S-N curve is a powerful tool for predicting the fatigue life of components and making informed design decisions.
S-N Curves for AISI 1045 Steel and 2024-T6 Aluminum Alloy
As shown in the S-N curve, the fatigue behavior of steel and aluminum differs significantly.
Steel
Steel, renowned for its versatility and excellent mechanical properties, is a workhorse material in countless engineering applications. For instance, plain carbon steel typically exhibits a fatigue strength of around 340 MPa for 10^7 cycles.
High-strength steels, commonly used in automotive and aerospace applications, can reach fatigue strengths of 700 MPa or higher for the same number of cycles, due to their specialized compositions and heat treatments.
Steel also boasts a well-defined fatigue limit, typically falling within the range of 0.4 to 0.5 times its ultimate tensile strength, below which it can theoretically endure a vast number of cycles without succumbing to fatigue failure.
Aluminum
Lightweight and possessing favorable strength-to-weight ratios, aluminum alloys are a popular choice for a wide range of engineering applications. However, unlike steel, aluminum alloys do not exhibit a clear fatigue limit due to their microstructure and deformation mechanisms.
S-N Curve comparison for steel and aluminum alloys.
The fatigue strength of aluminum alloys can vary significantly depending on the specific alloy, heat treatment, and processing conditions, with typical values ranging from 85 MPa to 135 MPa for 10^7 cycles.
Stainless Steel
Stainless steel, renowned for its exceptional corrosion resistance and robust mechanical properties, is a sought-after material for demanding applications. Its various types, such as austenitic, ferritic, martensitic, and duplex, offer a range of corrosion resistance properties due to their differing chromium and nickel contents.
The fatigue strength of austenitic stainless steel, the most common type, typically ranges from 300 MPa to 650 MPa for 10^7 cycles, depending on the specific grade and heat treatment. It also exhibits a fatigue limit that can vary depending on the grade, often falling within the range of 200-300 MPa.
Titanium
Titanium alloys are prized in engineering for their exceptional strength-to-weight ratio and remarkable fatigue properties, such as their inherent resistance to crack initiation and propagation, making them indispensable in demanding applications where weight reduction and durability are paramount.
For example, the widely used Ti-6Al-4V alloy, in its annealed condition, typically exhibits a fatigue strength of 450 to 590 MPa for 10^7 cycles.
Titanium alloys also have a fatigue limit that can vary depending on the specific alloy and its processing, often ranging from 350 to 500 MPa, allowing them to endure significant cyclic loads without failure, making them ideal for critical aerospace and biomedical applications.
Practical Applications and Design Considerations
With knowledge in fatigue data, engineers can predict how long a component will last under cyclic loading conditions and design accordingly. So, it involves selecting materials with appropriate fatigue properties and considering certain factors. They are stress concentration, surface finish, and environmental conditions.
A crucial aspect of fatigue design is the application of safety factors. Safety factors help to account for uncertainties in material properties, loading conditions, and environmental influences.
For example, if a component is expected to experience a maximum cyclic stress of 200 MPa, engineers might design it to withstand 250 MPa. This allows them to ensure it remains safe and functional even under unexpected conditions. Such a conservative approach helps prevent fatigue failure, which can lead to catastrophic consequences in applications.
Fatigue is a major concern in several key industries:
- Aircraft Structures: Significant cyclic loads during flight and landing subject components like wings, fuselages, and landing gears. Ensuring these parts have sufficient fatigue strength is vital for aircraft safety and longevity.
- Automotive Parts: Suspension systems, engines, and chassis components experience repetitive loading. Designing these parts with appropriate fatigue strength helps to prevent failure and ensure vehicle reliability.
- Bridges and Infrastructure: Structural elements of bridges and buildings endure cyclic loads due to traffic, wind, and other forces. Engineers must account for fatigue strength in design to maintain structural integrity over time.
For comprehensive fatigue testing and analysis, explore SDC Verifier’s advanced solutions to ensure your products meet the highest standards of safety and performance.