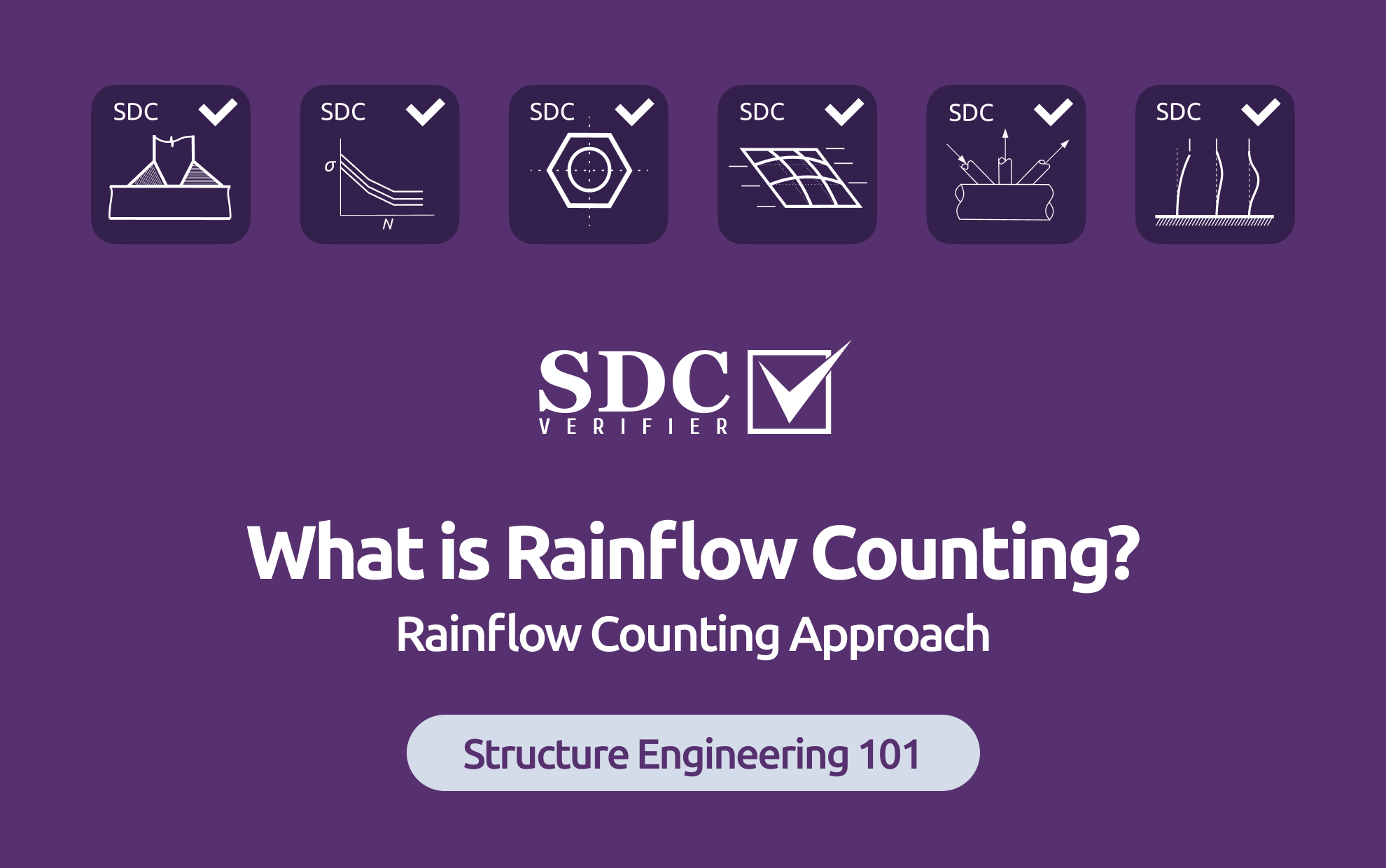
Fatigue analysis is a critical component of engineering design. It helps predict how materials and structures will perform under repeated loading conditions. The ability to anticipate and prevent fatigue failures can mean the difference between a safe, long-lasting product and a catastrophic failure.
One of the most effective techniques in fatigue analysis, especially for variable amplitude loading, is Rainflow Counting. This method allows engineers to break down complex loading histories into manageable cycles, providing valuable insights into potential fatigue damage. In this article, you’ll learn more about the Rainflow Counting approach.
This post continues the cycle of our previous articles: “What is Fatigue? Definitions, Types, Causes,” “Fatigue Strength and Limit: Understanding Materials-Specific Data,” “Fatigue Life: Key Influencing Factors and Advanced Prediction Methods.” It delves deeper into fatigue analysis, equipping you with the knowledge to tackle even the most challenging fatigue-related problems.
What is Rainflow Counting?
Rainflow Counting is a popular method in fatigue analysis that helps engineers analyze variable amplitude loading by breaking down complex, irregular stress histories into individual, simple stress cycles. This approach is precious because real-world loading conditions often involve fluctuating stresses. It’s challenging to predict fatigue life using fundamental, constant amplitude analysis. In the picture, you can see the example of Rainflow Counting:
Tatsuo Endo first developed the Rainflow Counting method in the 1960s to assess the durability of materials subjected to non-constant stress cycles, such as those experienced by automobiles, aircraft, and bridges. Endo’s work was founded on a more standardized approach to fatigue analysis, which was later formalized in the ASTM E1049 standard.
The purpose of Rainflow Counting is to simplify complex loading histories by counting the number of stress cycles contributing to fatigue damage. By identifying and categorizing these cycles, engineers can more accurately estimate the fatigue life of a component or structure. Rainflow Counting is vital for engineers to design safe, reliable products, accounting for stress cycles, predicting fatigue life, and enhancing overall safety and durability.
Understanding Variable Amplitude Loading
Variable amplitude loading is the type of loading that structures or materials experience when the magnitude and frequency of the applied loads vary over time. This contrasts with constant amplitude loading, where the load magnitude remains consistent throughout the loading cycles.
In real-world engineering applications, components are rarely subjected to uniform loads. Instead, they experience fluctuating stresses and strains due to varying operational conditions. For instance, the load on an aircraft wing changes continuously during flight due to turbulence, maneuvers, and changes in altitude.
The analysis of variable amplitude loading presents significant challenges. Unlike constant amplitude loading, where the fatigue life of a component can be more straightforwardly predicted, variable amplitude loading involves complex interactions between different stress levels. If not properly accounted for, these interactions can lead to unexpected failures. The non-uniform nature of the loading sequence can accelerate damage accumulation, making traditional fatigue analysis methods less effective.
This is where Rainflow Counting comes into play. As a specialized method in fatigue analysis, Rainflow Counting is designed to decompose complex, variable amplitude loading into more straightforward cycles that can be analyzed more easily. By breaking down these loads into individual cycles, engineers can apply methods like Miner’s rule to predict the fatigue life of a component more accurately.
The Rainflow Counting Algorithm
Here’s a step-by-step explanation of the Rainflow Counting algorithm, complemented by diagrams to illustrate the process:
- Plot the Load History: Start by plotting the component’s stress or strain history of against time. This plot shows how the load varies during the analysis period.
- Identify Hysteresis Loops: Look for “hysteresis loops” in the load history. These loops are formed by alternating load peaks and valleys, representing a complete loading and unloading cycle.
Hysteresis Loop:
- Peak: The highest stress level within the loop.
- Valley: The lowest stress level within the loop.
- Decompose the History into Cycles: To count the number of cycles, decompose the load history into individual hysteresis loops. Each loop represents a stress cycle with specific maximum and minimum values. (Source: Application of the Rainflow Counting Method in Fatigue).
- Apply the Rainflow Counting Rules:
- Cycle Counting: For each hysteresis loop, identify the peaks and valleys. Count each loop as a separate cycle, noting the amplitude (half the difference between the peak and valley) and the mean stress (average of the peak and valley).
- Overlay Method: In complex load histories, overlay the loops to identify and count overlapping cycles. This ensures that all significant stress cycles are accounted for.
- Summarize the Results: After counting all cycles, summarize the results into a table or histogram showing the number of cycles at different stress amplitudes. This data can then be used to apply fatigue analysis methods, such as Miner’s rule.
Rainflow Counting in Fatigue Analysis
Rainflow Counting is particularly valuable when dealing with variable amplitude loading. This method quantifies the number of stress cycles in a complex load history, which is essential for predicting the fatigue damage a component will experience over time.
The S-N Curve and Its Role in Fatigue Life Prediction
The S-N curve is used to predict the fatigue life of a component by comparing the stress amplitudes obtained from Rainflow Counting with the curve. Higher stress amplitudes typically correlate with fewer cycles to failure, while lower amplitudes suggest a longer fatigue life.
Combining Rainflow Counting Results with the S-N Curve
Once the Rainflow Counting algorithm has been applied, the resulting data is summarized in a Rainflow Matrix, which details the number of cycles at each stress amplitude. This matrix is then used in conjunction with the S-N curve to estimate the component’s fatigue life. By mapping the stress amplitudes from the Rainflow Matrix onto the S-N curve, engineers can determine the expected number of cycles to failure for each stress level.
Miner’s Rule and Accumulating Fatigue Damage
Miner’s Rule is a commonly used method for accumulating fatigue damage from different stress levels. It works by summing the fraction of life consumed by each stress cycle, based on the S-N curve data. If the total damage reaches a value of 1, the component has reached its fatigue limit and is expected to fail. This approach allows for a comprehensive assessment of fatigue damage across varying loading conditions.
Advantages and Limitations of Rainflow Counting
Rainflow Counting is one of the most robust methods for analyzing component fatigue subjected to variable amplitude loading. Its strengths lie in its ability to accurately decompose complex load histories into individual stress cycles, making it invaluable in real-world engineering applications where loading conditions are rarely uniform.
Advantages of Rainflow Counting
Here are some of the key benefits:
- Handling Complex Load Histories: Rainflow Counting is helpful in complex load histories, such as those found in automotive, aerospace, and civil engineering structures, as it effectively counts cycles and understands stress levels contributing to fatigue.
- Industry Standard: Engineers use this method in various industries for its reliability and accuracy. It is often incorporated into design codes like ASTM E1049 for consistent fatigue analysis practices.
- Compatibility with Fatigue Life Prediction Models: Rainflow Counting is a popular choice for engineers due to its compatibility with fatigue life prediction models like the S-N curve and Miner’s Rule.
- Implementation in Software Programming: For this process typically uses software like MATLAB, with some fatigue analysis tools that integrate Rainflow Counting directly, such as Rainflow Counting Tool. Large datasets are managed through databases such as SQL Server. (Source: Application of the Rainflow Counting Method in Fatigue).
Limitations of Rainflow Counting
Despite its strengths, Rainflow Counting is not without its limitations:
- Sensitivity to Noise: The method’s sensitivity to noise in loading data can lead to spurious cycles and overestimation of fatigue damage, especially when data isn’t properly filtered or smoothed.
- Computational Complexity: For large datasets, especially those with long load histories or high-frequency data, the computational effort required to apply Rainflow Counting can become significant.
- Simplification Assumptions: Rainflow Counting, though powerful, may need to be more accurate in fatigue life predictions due to assumptions like linear material behavior under cyclic loading.
Comparison with Other Fatigue Analysis Methods
Rainflow Counting differs significantly from other traditional fatigue analysis methods:
Goodman Diagram
Purpose: Evaluate fatigue life under combined mean stress and alternating stress.
Comparison: Rainflow Counting is preferred when dealing with variable amplitude loading, while the Goodman method is more suited to constant amplitude situations.
Here are the Rainflow Counting analysis and Goodman-diagram procedure results, for example (source: ResearchGate):
S-N Curve Method
Purpose: Provides fatigue life prediction based on stress (S) and number of cycles (N).
Comparison: Rainflow Counting extends the S-N curve method by accounting for the sequence and magnitude of variable loading, whereas the S-N curve alone is limited to constant amplitude loading.
Fourier Transform Method
Purpose: Analyzes stress signals in the frequency domain.
Comparison: Rainflow Counting operates in the time domain, making it more intuitive for handling real-world loading conditions directly.
Why is Rainflow Counting Preferred Over Other Methods?
Engineers prefer Rainflow Counting over fatigue analysis methods, such as the Goodman Diagram or S-N curve method, when dealing with variable amplitude loading. Unlike methods that assume constant amplitude loading, Rainflow Counting effectively identifies and counts individual load cycles within complex, irregular loading histories.
This makes it especially useful in real-world engineering applications, where loads rarely remain constant and fluctuate unpredictably. By accurately capturing the sequence and magnitude of these cycles, Rainflow Counting provides a more precise assessment of fatigue damage, leading to more reliable predictions of component life under variable loading conditions.
Sum Up
Rainflow Counting accurately predicts how components will handle fluctuating stresses over their lifetime. This method helps engineers understand how materials respond to real-world conditions by breaking down complex loading patterns into more straightforward stress cycles. It’s precious for analyzing situations where loads are not constant, such as in aircraft, bridges, or machinery.
By clearly showing how different stress levels affect a component’s durability, Rainflow Counting helps design safer and more reliable products. While it may have some limitations, such as sensitivity to data noise and computational demands, its ability to handle variable amplitude loading makes it an influential tool in fatigue analysis.