What is Fatigue? Definitions, Types, Causes
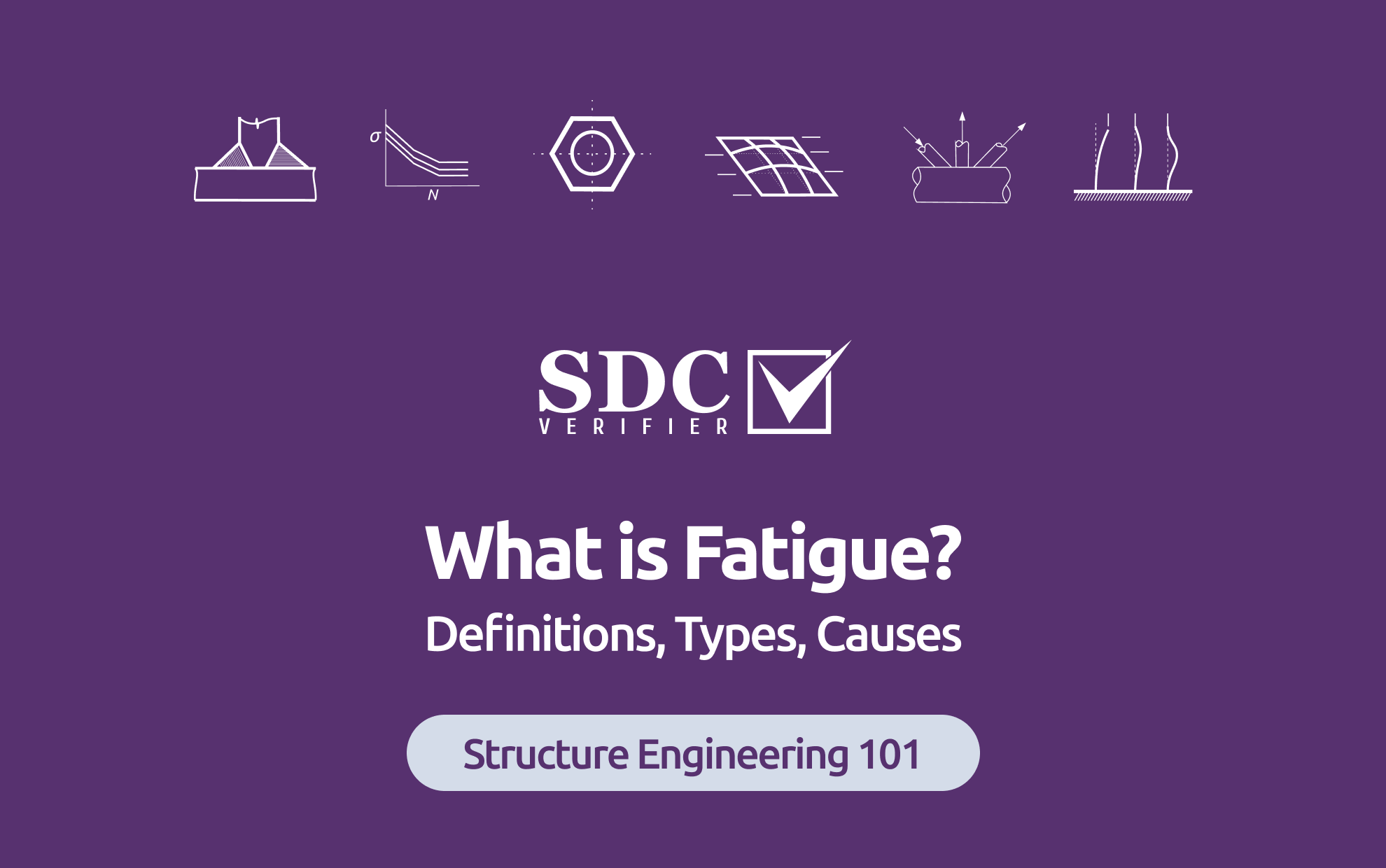
What exactly is fatigue? How does it develop, and why is it so difficult to detect? In this comprehensive guide, we’ll into the world of fatigue engineering, exploring its various types, causes, and methods of prevention.
What is Fatigue?
Fatigue is defined as the weakening and eventual failure of a material due to repeated or fluctuating stresses. These stresses are often well below the material’s ultimate tensile strength, making fatigue a particularly insidious threat.
Key Concepts: The Fatigue Cycle
To understand fatigue, we must first grasp the concept of a stress cycle. A stress cycle consists of the repeated loading and unloading of a material, much like bending a paperclip back and forth. Each cycle introduces microscopic damage, accumulating over time and ultimately leading to the formation of cracks.
Crack Initiation and Propagation
The fatigue process begins with the initiation of a tiny crack, often at a microscopic defect or stress concentration point within the material. As stress cycles continue, this crack gradually propagates or grows, steadily weakening the structure. The crack’s propagation rate depends on various factors, including the magnitude and frequency of the stress, the material’s properties, and environmental conditions.
In the initial stages, fatigue damage is often invisible to the naked eye, making it difficult to detect without specialized techniques like non-destructive testing. However, as the crack propagates and reaches a critical size, catastrophic failure can occur suddenly and without warning.
Why Fatigue Matters
Understanding the mechanisms of fatigue is crucial for engineers because it enables them to design structures and components that can withstand the rigors of repeated loading. By selecting appropriate materials, optimizing designs, and implementing regular inspections, engineers can mitigate the risk of fatigue failures, ensuring the safety and longevity of everything from airplanes to bridges to medical implants.
Types of Fatigue
forestay crack
Fatigue is not a one-size-fits-all phenomenon. It manifests in different forms depending on the nature of the stress cycles and the material’s response. Let’s explore some of the most common types of fatigue encountered in engineering:
High-Cycle Fatigue (HCF)
High-cycle fatigue occurs when a material is subjected to a large number of stress cycles, typically in the millions or even billions, with each cycle causing relatively low stress levels. This type of fatigue is often associated with components that experience vibrations or rotating motions, such as turbine blades, engine crankshafts, and gear teeth. The failure in HCF usually initiates below the surface and gradually propagates inward.
Low-Cycle Fatigue (LCF)
In contrast to HCF, low-cycle fatigue involves a smaller number of stress cycles, often in the hundreds or thousands, but with each cycle causing significant plastic deformation. This type of fatigue is common in structures that experience high loads or extreme temperature fluctuations, such as pressure vessels, nuclear reactors, and offshore platforms. LCF cracks often initiate on the surface and grow rapidly.
Thermal Fatigue
Thermal fatigue arises from repeated heating and cooling cycles, causing thermal expansion and contraction within a material. This can induce significant stresses, especially in components with constrained geometries or those made of materials with differing thermal expansion coefficients. Examples include turbine blades, heat exchangers, and brake discs.
Corrosion Fatigue
Image of a corroded metal surface or a structure affected by environmental factors.
Corrosion fatigue is a particularly destructive form of fatigue that occurs when a material is subjected to cyclic loading in a corrosive environment. The combined action of stress and corrosion accelerates crack initiation and propagation, leading to premature failure. This type of fatigue is a major concern in marine structures, chemical processing equipment, and underground pipelines.
Causes of Fatigue
Let’s examine the primary culprits behind fatigue failure:
Types of cyclic loading: Fully-reversed (top) and zero-based (bottom) stress cycles.
1. Cyclic Loading
The most fundamental cause of fatigue is cyclic loading, the repeated application and removal of stress on a material. This can occur due to vibrations, rotating machinery, pressure fluctuations, or any other dynamic force that induces stress cycles. The greater the magnitude and frequency of these cycles, the faster fatigue damage accumulates.
Example: A bridge experiences cyclic loading from the weight of passing vehicles, leading to fatigue cracks in its structural components over time.
2. Material Defects
Materials are not perfectly uniform, and often contain microscopic defects such as inclusions, voids, or grain boundaries. These imperfections act as stress concentrators, amplifying the local stress levels and initiating cracks more easily. The type and distribution of defects can significantly influence a material’s fatigue resistance.
Example: A weld seam in a pressure vessel contains microscopic pores that act as stress concentrators, leading to fatigue cracking under cyclic pressure.
3. Environmental Factors
The environment in which a component operates can accelerate fatigue damage. High temperatures can reduce a material’s fatigue strength, while corrosive environments can initiate cracks through chemical reactions. Even seemingly benign factors like humidity or exposure to sunlight can contribute to fatigue over time.
Example: A turbine blade operating in a high-temperature environment experiences thermal fatigue, leading to cracks and reduced service life.
4. Design Flaws
Poor design choices can inadvertently create conditions that promote fatigue failure. Sharp corners, abrupt changes in cross-section, or inadequate stress relief can all lead to stress concentrations that accelerate crack initiation. Furthermore, ignoring the potential for fatigue during the design process can result in components that are simply not robust enough to withstand the expected loading conditions.
Example: A poorly designed bicycle frame with a sharp notch near the seat post experiences stress concentration, leading to fatigue failure under normal riding conditions.
Calculating and Predicting Fatigue
While fatigue equations offer a theoretical framework for prediction, engineers must also consider the allowable fatigue stress for a given material, which defines the safe stress limits that can be endured over a specific number of cycles before failure occurs.
Fatigue Equations
S-N curve (stress-life curve) illustrating the relationship between stress amplitude and the number of cycles to failure for a material. Engineers use this data to predict fatigue life and assess the risk of failure under cyclic loading.
Several mathematical models have been developed to approximate a material’s fatigue behavior. Some of the most commonly used equations include:
Goodman Diagram
This graphical representation helps engineers determine the allowable stress amplitude for a given mean stress level to avoid fatigue failure.
Soderberg Equation
Similar to the Goodman Diagram, this equation accounts for both mean and alternating stresses to predict fatigue life.
Miner’s Rule
This cumulative damage model calculates the total damage a material accumulates under varying stress levels and predicts when failure is likely to occur.
While these equations provide valuable insights, it’s important to note that they are simplified models and may not always perfectly reflect real-world conditions.
Fatigue Testing
To complement theoretical calculations, fatigue testing is essential for validating a material’s fatigue properties and ensuring the accuracy of predictions. By subjecting specimens to controlled cyclic loading, engineers can observe crack initiation and propagation firsthand, gaining valuable data on fatigue life, crack growth rates, and failure modes.
Finite Element Analysis (FEA)
In recent years, Finite Element Analysis (FEA) has emerged as a powerful tool for fatigue prediction. By creating a virtual model of a component or structure in SDC Verifier, engineers can simulate the effects of cyclic loading and identify potential stress concentrations or areas of weakness that could lead to fatigue failure. FEA enables engineers to optimize designs before physical prototypes are even built, saving time and resources while improving overall reliability.
By combining theoretical calculations, experimental testing, and advanced simulation techniques, engineers can gain a comprehensive understanding of a material’s fatigue behavior, enabling them to design safer, more durable products and structures that can withstand the test of time.
To further enhance fatigue predictions, engineers can leverage sophisticated fatigue calculation tools that integrate FEA results with established fatigue models, accelerating the design optimization process.
Preventing Fatigue Failures
Preventing fatigue failures is a multifaceted challenge that requires a holistic approach, encompassing design, manufacturing, and maintenance practices.
Design Considerations
Material Selection: Choosing the right material is paramount. Materials with high fatigue strength, such as certain alloys or composites, can withstand more stress cycles before failure.
Stress Reduction: Minimizing stress concentrations is key to preventing crack initiation. This can be achieved through careful design, avoiding sharp corners, notches, or abrupt changes in geometry. Techniques like fillets, radii, and gradual transitions can help distribute stress more evenly.
Surface Finishing: Smooth surfaces are less prone to crack initiation than rough ones. Applying surface treatments like shot peening or polishing can improve fatigue life by introducing compressive residual stresses that counteract the tensile stresses from cyclic loading.
Manufacturing Practices: Ensuring Quality and Consistency
Quality Control: Rigorous quality control measures during manufacturing are essential to detect and eliminate defects that could act as stress concentrators. This includes inspecting raw materials, monitoring welding processes, and verifying final product dimensions.
Non-Destructive Testing (NDT): NDT techniques like ultrasonic testing, X-ray radiography, or magnetic particle inspection can reveal hidden flaws or cracks that may not be visible to the naked eye. Regular NDT inspections can help identify potential fatigue damage before it leads to catastrophic failure.
Adhering to recognized fatigue design standards, such as DIN 15018 fatigue, can provide engineers with valuable guidance on material selection, stress analysis, and safety factors, ultimately leading to more robust and reliable designs.
Maintenance and Inspection
Regular Inspections: Implementing a schedule of regular inspections allows for early detection of fatigue cracks, enabling timely repairs or replacements before the damage becomes critical.
Monitoring: Using sensors to monitor stress levels, vibration, and other relevant parameters can provide valuable insights into a component’s condition and alert engineers to potential fatigue issues.
Predictive Maintenance: By analyzing data from inspections and monitoring systems, engineers can predict when a component is nearing the end of its fatigue life and schedule maintenance or replacement proactively, minimizing the risk of unexpected failures.
Beyond routine inspections, adopting a proactive approach like residual life analysis can be invaluable in predicting the remaining fatigue life of crane structures, enabling timely interventions to prevent cracks and potential failures.
Fatigue may be a persistent challenge, but with careful planning and diligent execution, it can be effectively managed to safeguard our engineered world.
Interested in simplifying your fatigue analysis? Discover how SDC Verifier can make a difference in your engineering projects.