AS 4100. Example 4: Determine the Design Section Capacity for a Concentrically Loaded Member in Compression
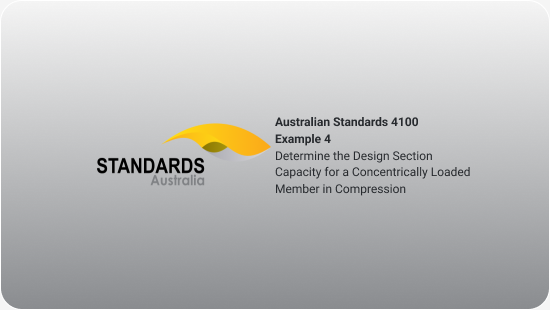
This benchmark was prepared based on
Australian Steel Institute (ASI) Steel Structures – Sample Worked Problems to AS 4100
using
SDC for Femap and Simcenter Femap Version 2022.2
Ensure the accuracy of your calculations for concentrically loaded compression members under AS 4100 guidelines. This benchmark covers input parameters, modeling in FEA software (addressing its limitations), and results analysis using SDC Verifier 2024 R1.
Based on the input parameters presented above a beam model was created with the following material and property definitions:
Note: Because of the limitations of the FEA software the cross-section is defined without fillets, so slight differences in geometrical properties are to be expected.
Where possible these values have been modified manually (as for the moments of inertia І1 and І2, torsion constant and warping constant in the table above), but some are calculated internally without the possibility to modify them (e.g. plastic section modulus).
Additionally, the yield stress is defined with one value for the beam property, so it’s the same for both the web and the flange, while in the problem definition, there is one value for the flange – 300 MPa, and a different value for the web – 320 MPa, so the lesser value was chosen.
The above parameter is checked within a Property Check, in this case, one defined for I-Beam cross-sections.
As we can see the form factor value matches completely.
Nominal section capacity also matches with the value in the example. We can also see the properly assigned effective lengths.
SDC Verifier automatically picks the controlling axis for buckling when calculating the member slenderness values.
We can see that the value of the member’s slenderness matches as well
The compression member section constant ab is defined as a characteristic based on the according table:
The member slenderness reduction factor ac is calculated automatically through the procedure that doesn’t require input from tables:
Which results in an almost identical value as when using the linear interpolation based on Table 6.3.3(3) in the example.
When calculating the nominal member capacity in compression (N_c) SDC Verifier follows the logic of the standard, so the multiplication by the capacity factor ф happens later when comparing it to the design axial compression force.
That’s why the value obtained in the table has to be additionally reduced by ф for the purposes of the calculations in this example:
ф∗Nc=0.9∗2129202 N=1916 kN
As we can see the obtained value is slightly higher than in the example, but that is due to the member slenderness reduction factor also being slightly higher, because of the manual way of obtaining that value from the table in the example.
Reliable Results for AS 4100 Concentric Compression Design
While minor discrepancies may exist due to FEA software limitations, this benchmark demonstrates SDC Verifier’s alignment with AS 4100 standards for calculating Design Section Capacity in compression members. Understanding these nuances empowers you to confidently validate your designs.
This post uses screenshots from the Steel Structures Sample Worked Problems to AS 4100 document