UR S35 Plate Buckling Benchmark: Hand Calculations vs. SDC Verifier
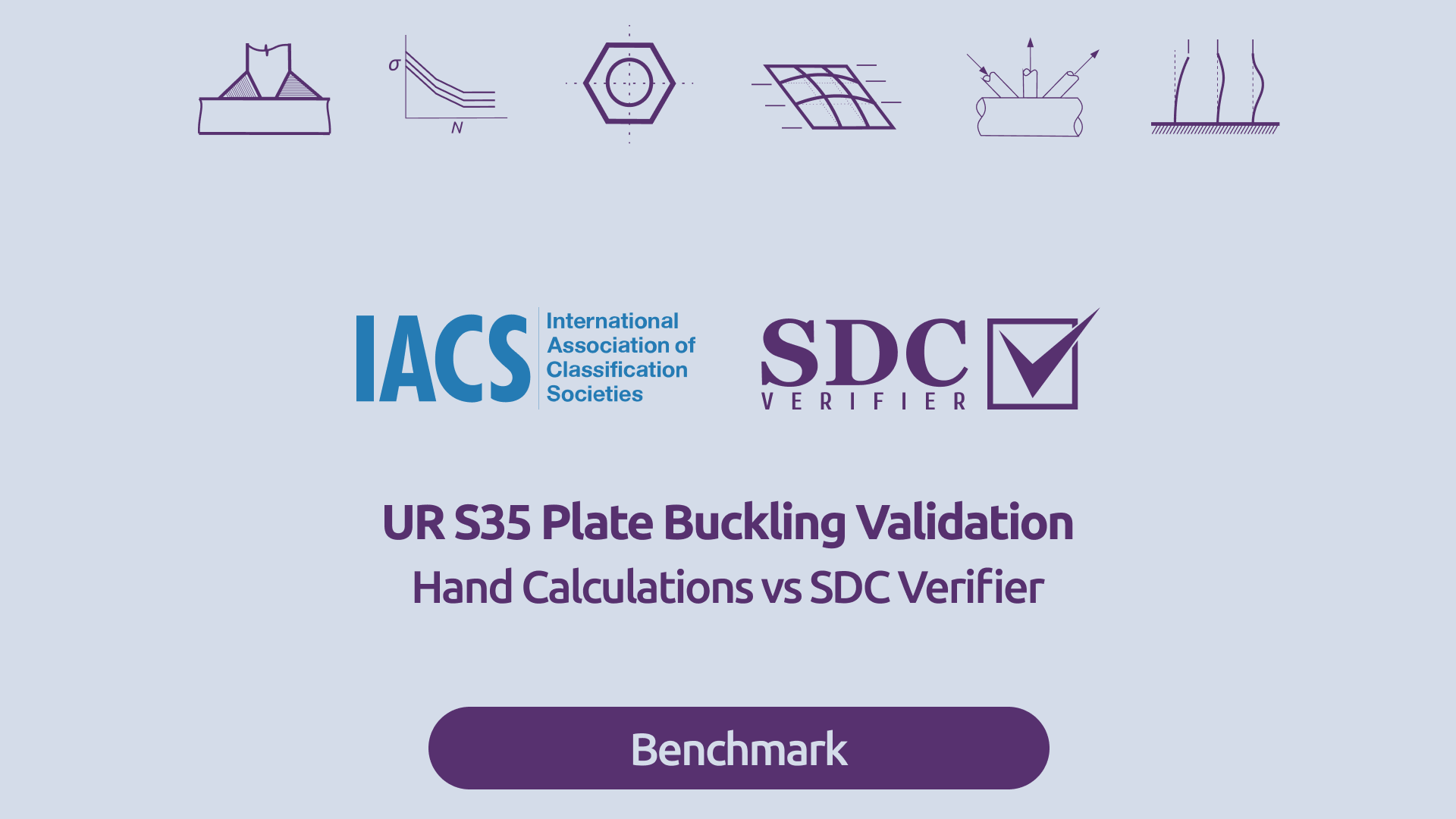
This benchmark evaluates the implementation of the UR S35 Plate Buckling standard (February 2023, Corr. 1 Sep. 2024) using a finite element model built and checked in SDC Verifier. A steel plate model with dimensions 10.2 × 5.4 × 1.1 meters was created and loaded with realistic force cases to simulate buckling conditions. The goal of this benchmark is to validate SDC Verifier’s implementation against calculations performed manually, based on UR S35 methodology.
The model setup includes accurate material properties, realistic boundary conditions, and a clear application of loads across the top plate. Hand calculations were carried out step-by-step, applying all relevant code equations and intermediate factors to determine the ultimate buckling stresses and utilization factor. These results were then compared with the automatic check in SDC Verifier.
A test plate model with 10.2 × 5.4 × 1.1 m dimensions was designed for the purpose of this benchmark:
The model was constrained at four bottom corners where side plates are connected.
Forces were applied on the edges of the top plate with the following values:
- |𝐹ₗ⁺| = |𝐹ₗ⁻| = 3000 kN
- |𝐹ₛ⁺| = |𝐹ₛ⁻| = 2550 kN
- |𝐹ₚ⁺| = |𝐹ₚ⁻| = 2500 kN
One of the top plates was chosen for all the calculations included in the check.
The plate dimension:
-
Length: a = 3.400 m
-
Width: b = 1.350 m
-
Thickness: tₚ = 0.012 m
The plate material – mild steel properties:
-
Young’s Modulus: E = 210 GPa
-
Poisson’s Ratio: ν = 0.3
-
Mass Density: ρ = 7850 kg/m³
-
Tensile Strength: Rₘ = 360 MPa
-
Yield Stress: RₑH,P = 235 MPa
Due to the complexity of the model, all required stress values were obtained with the help of FEM.
Obtained values:
-
σₓ = 37.14 MPa
-
σᵧ = 25.12 MPa
-
τ = 16.34 MPa
Calculations
In order to check the results, analytical calculations were first carried out.
Final equations for limit states according to code (Sec. 5 / [2.2.1]):
I.
(γ1σxSσx)e0−B(γ1σxSσx)e0/2(γ1σySσy)e0/2+(γ1σySσy)e0+(γ1∣τ∣Sτc)e0=1
II. (when σx≥0sigma_x geq 0)
(γ2σxSσx)2/βp2.5+(γ2∣τ∣Sτc)2/βp2.5=1
III. (when σy≥0sigma_y geq 0)
(γ3σySσy)2/βp2.5+(γ3∣τ∣Sτc)2/βp2.5=1
IV.
γ4∣τ∣Sτc=1
Aspect Ratio of the Plate Panel (Sec. 5 / Symbols):
α=ab=3.401.35=α=2.519
Elastic Buckling Reference Stress (Sec. 5 / Symbols):
σE=π2E12(1−ν2)(tpb)2sigma_E = frac{pi^2 E}{12(1 – nu^2)} left( frac{t_p}{b} right)^2
σE=π2⋅210⋅10912⋅(1−0.32)(0.0121.35)2=σE=1.499×106 Pa
Edge Stress Ratio
As defined in Sec. 5 / Symbols, the edge stress ratio was set in both directions as 1.
Stresses are calculated using a weighted average approach (App. 1 / [2.2.1]).
Correction factor F<sub>long</sub> (Sec. 5 / [2.2.4]) was set as 1 (Sec. 5 / Table 2):
Flong=1
Correction factor F<sub>tran</sub> (Sec. 5 / [2.2.5]) was set as 1:
Ftran=1
Ultimate Buckling Stresses – Case 1
(Calculated according to Sec. 5 / Table 3)
Compression Setup:
Top plate compressed in x-direction with edge stress ratio:
ψ=1
Intermediate Parameters:
Effective width factor
c=min((1.25−0.12⋅ψ),1.25)=min(1.13,1.25)=1.13
Slenderness parameter
λc=c2(1+1−0.88c)=1.132(1+1−0.881.13)lambda_c = frac{c}{2} left(1 + sqrt{1 – frac{0.88}{c}}right) = frac{1.13}{2} left(1 + sqrt{1 – frac{0.88}{1.13}}right)λc=0.831
Buckling coefficient in x-direction
Kx=Flong⋅8.4ψ+1.1=1⋅8.41+1.1=4
Reference Degree of Slenderness in x-direction
(Sec. 5 / [2.2.2])
λx=ReH,PKx⋅σE=235⋅1064⋅1.4996549⋅106=1.979
Reduction Factor for Stress in x-direction
(Sec. 5 / Table 3)
Cx=c(1λx−0.22λx2)=1.13⋅(11.979−0.22(1.979)2)=0.507
Ultimate Buckling Stresses – Case 2
(Calculated according to Sec. 5 / Table 3)
Compression Setup:
Top plate compressed in y-direction with edge stress ratio:
ψ=1
Intermediate Parameters:
Effective width factor
c=min((1.25−0.12⋅ψ),1.25)=min(1.13,1.25)=1.13
Slenderness parameter
λc=c2(1+1−0.88c)=1.132(1+1−0.881.13)lambda_c = frac{c}{2} left(1 + sqrt{1 – frac{0.88}{c}}right) = frac{1.13}{2} left(1 + sqrt{1 – frac{0.88}{1.13}}right)
λc=0.831
Parameter
f1=(1−ψ)(α−1)=(1−1)(2.519−1)=0
Buckling coefficient in y-direction
Ky=Ftran⋅2(1+1α2)21+ψ+1−ψ100⋅(2.4α2+6.9f1)K_y = F_{tran} cdot frac{2 left(1 + frac{1}{alpha^2}right)^2}{1 + psi + frac{1 – psi}{100} cdot left( frac{2.4}{alpha^2 + 6.9 f_1} right)}
Ky=1⋅2(1+12.5192)21+1+1−1100⋅(2.42.5192+6.9⋅0)=1.340
Reference Degree of Slenderness in y-direction
(Sec. 5 / [2.2.2])
λy=ReH,PKy⋅σE=235⋅1061.340⋅1.4996549⋅106=3.419
Factor c1c_1
(Sec. 5 / [2.2.3], based on SP-A assessment method)
c1=(1−1α),c1≥0c_1 = left(1 – frac{1}{alpha}right), quad c_1 geq 0
c1=1−12.519=0.603
R=0.220
Conditions for λp2lambda_p^2 Based on Slenderness:
λp2=λy2−0.5and1≤λp2≤3
λp2=3.4192−0.5and1≤λp2≤3
λp2=3
Correction Factor FF – Conditional Forms
-
General formula:
F=(1−(Ky0.91−1)λp2)⋅c1andF≥0
-
Substituted for Case 2:
F=(1−(1.3400.91−1)3)⋅0.603andF≥0
-
Result:
F=0.508
Calculation of Parameter TT
General Formula:
T=λy+1415λy+13
Substituted Values:
T=3.419+1415⋅3.419+13
Result:
T=4.026
Calculation of Parameter HH
General Formula:
H=λy−2λyc(T+T2−4)andH≥R
Substituted Values:
H=3.419−2⋅3.4191.13⋅(4.026+4.0262−4)andH≥0.22
Result:
H=2.614
Reduction Factor for Stress in y-direction CyC_y
(Sec. 5 / Table 3)
General Formula:
Cy=c(1λy−R+F2(H−R)λy2)
Substituted Values:
Cy=1.13⋅(13.419−0.22+0.5082⋅(2.614−0.22)3.4192)
Result:
Cy=0.250
Case 15: Shear Buckling in xy Direction
Shear Buckling Coefficient KτK_tau
General Formula:
Kτ=3(5.34+4α2)
Substituted:
Kτ=3(5.34+42.5192)=10.341
Reference Degree of Slenderness λτlambda_tau
(Sec. 5 / [2.2.2])
λτ=ReH,PKτ⋅σElambda_tau = sqrt{ frac{R_{eH,P}}{K_tau cdot sigma_E} }
λτ=235⋅10610.341⋅1.4996549⋅106=1.231
Reduction Factor for Shear Stress CτC_tau
(Sec. 5 / Table 3)
Cτ=0.84λτ=0.841.231=0.682
Ultimate Buckling Stresses
(Calculated according to Sec. 5 / [2.2.3])
In the direction parallel to the longer edge of the buckling panel:
σcx=Cx⋅ReH,P=0.507⋅235 MPa=119.145 MPa
In the direction parallel to the shorter edge of the buckling panel:
σcy=Cy⋅ReH,P=0.250⋅235 MPa=58.750 MPa
Shear Buckling Stress:
τc=Cτ⋅ReH,P3=0.682⋅235 MPa3=92.532 MPa
Calculation of Plate Slenderness Parameter βpbeta_p
(Sec. 5 / [2.2.1])
General Formula:
βp=btpReH,PE
Substituted Values:
βp=1.3500.012⋅235⋅106210⋅109
Result:
βp=3.763
Coefficient BB
(According to Sec. 5 / Table 1)
General Formula:
B=0.7−0.3⋅βpα2
Substituted Values:
B=0.7−0.3⋅3.7632.5192
Result:
B=0.522
Coefficient e0e_0
(According to Sec. 5 / Table 1)
General Formula:
e0=2βp0.25
Substituted Values:
e0=23.7630.25
Result:
e0=1.436
Final Equations for Limit States
(Transformed from Sec. 5 / [2.2.1] to calculate stress multiplier factors acting on loads γgamma)
I.
γc1=(1(σxSσcx)e0−B(σxSσcx)e0/2(σySσcy)e0/2+(σySσcy)e0+(∣τS∣τc)e0)1e0
II.
γc2=(1(σxSσcx)2/βp0.25+(∣τS∣τc)2/βp0.25)βp0.25/2
III.
γc3=(1(σySσcy)2/βp0.25+(∣τS∣τc)2/βp0.25)βp0.25/2
IV.
γc4=τc∣τS∣
Partial Safety Factor
(Sec. 5 / Symbols)
S=1S = 1
Calculated Values of Stress Multiplier Factors γgamma:
I.
γc1=1.763
II.
γc2=2.486
III.
γc3=1.968
IV.
γc4=5.663
Failure Criterion
The minimum stress multiplier factor among all calculated values is used as the stress multiplier factor at failure:
γc=min(γc1,γc2,γc3,γc4)=1.763
Utilization Factor ηacteta_{act}
(Sec. 1 / [3.2.2])
Formula:
ηact=1γc
Substituted:
ηact=11.763
Result:
ηact=0.567
Material Setup and SDC Verifier Check
In SDC Verifier, the standard was added using the same material assumptions, and the check was performed accordingly.
1. Mild Steel Properties
Top Plate Properties (T = 12 mm)
Properties Summary
Calculated for the CSys “0..Basic Rectangular”
FEM Loads – Long Edges
This section contains information about the applied loads to the model.
FEM Loads – Short Edges
This section contains information about the applied loads to the short edges of the model.
FEM Loads – Long Edges Parallel
This section describes the applied loads along the long edges in the Y-direction.
Constraints
This section provides information about constrained parts of the model.
Results: Job 1 – Load Set ‘1’
UR S35 Plate Buckling (2023)
Implementation according to UR S35 Buckling Strength Assessment of Ship Structural Elements, February 2023 (Corr. 1 Sep. 2024)
Unit System
-
MKS (Meter / Kilogram / Second)
-
Standards referenced: API RP 2A, ISO 19902, NORSOK N004, DIN 15018, FEM 1.001, Eurocode3.
Intermediate Results of Ultimate Buckling Stresses
Results Comparison: Hand Calculations vs. SDC Verifier Check
Ultimate Buckling Stresses [MPa]
Parameter | Hand Calculations | SDC Verifier |
---|---|---|
σcx | 119.145 | 119.252 |
σcy | 58.750 | 58.631 |
τc | 92.932 | 92.585 |
Inverse of Stress Multiplier Factors Acting on Loads
Parameter | Hand Calculations | SDC Verifier |
---|---|---|
1 / γc1 | 0.567 | 0.562 |
1 / γc2 | 0.402 | 0.396 |
1 / γc3 | 0.508 | 0.504 |
1 / γc4 | 0.177 | 0.169 |
Utilization Factor
ηact = 1 / γc1 | 0.567 (Hand) | 0.562 (SDC Verifier) |
Results from SDC Verifier are consistent with those obtained from hand calculations, validating the accuracy of the model and the implementation of UR S35 plate buckling checks.
Conclusion
The comparison demonstrates a high level of agreement between hand calculations and the results obtained using SDC Verifier. Deviations in computed stresses and utilization factors remained within a negligible margin, confirming both the correctness of the analytical approach and the integrity of the implemented standard in SDC Verifier. This benchmark provides strong confidence in using SDC Verifier for UR S35 plate buckling assessments in real-world structural analysis scenarios.