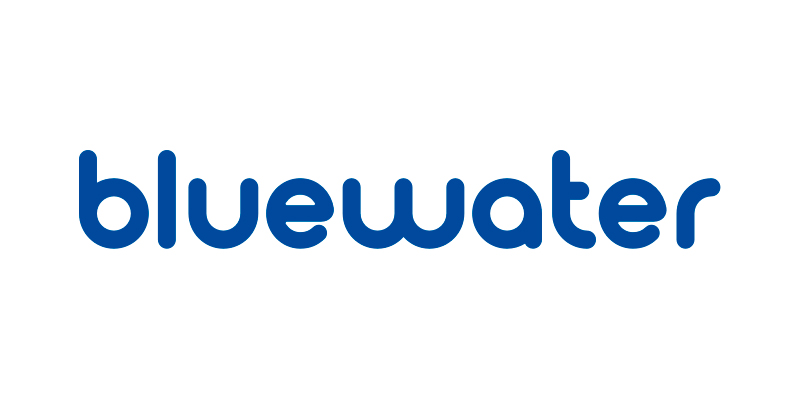
Bluewater Energy Services B.V. uses SDC Verifier for Haewene Brim FPSO evaluation in Lifetime Extension project

300+
load combinations for ULS, blast, heel & fatigue
- The project focuses on the structural evaluation of the P20 topside module on Bluewater’s Haewene Brim FPSO as part of a Lifetime Extension initiative.
- Using ANSYS Workbench and SDC Verifier, engineers performed strength, fatigue, and buckling checks based on DNV and Eurocode standards, modeling with both beam and shell elements.
- Advanced load combinations (approx. 300) ensured accurate simulation of multiple scenarios, confirming the module’s safety and serviceability after a significant weight increase to 630t.
Our long-term customer – Bluewater Energy Services B.V., specializes in the design, development, lease, and operation of tanker-based production and storage systems. The company owns and operates a fleet of high specification FPSOs designed to work in the harshest environmental conditions and under the most stringent regulatory regimes.
Floating Production Storage and Offloading (FPSO) is a core element of the oil & gas extraction and refinement process. FPSO is equipped with processing equipment for the separation, storage, and offloading of oil and gas from sub-sea oil wells or platforms. When oil and gas are processed, they are safely stored in the FPSO until offloading onto a tanker or a pipeline for transportation ashore.
Haewene Brim – Bluewater Energy Services B.V.’s FPSO has been in operation since 1999 on the Pierce and since 2014 also on the Brynhild field. Starting December 2021, Haewene Brim undergoes modifications, amongst others to the P20 topside module. A few years before Bluewater Energy Services B.V. used SDC Verifier to re-assess the strength and fatigue of the P20 Module – a separation unit located topside on the main deck under the latest DNV rules for topsides in Lifetime Extension project.
In 2013, P20 Module was already upgraded, adding an extra 110t of material. With 630t, it has been one of the heaviest Modules on board.
Using ANSYS Workbench in combination with SDC Verifier, the engineering team checked many aspects in one project.
- P20 Module was modeled with both beam elements and shell elements. Members/profiles were modeled with beam elements and verified via member checks in SDC Verifier. The member checks were performed in accordance with the Eurocode using the load factors from DNV-OS-C101. The load combinations were in accordance with DNV-OS-C102 (Structural design of offshore ship-shaped and cylindrical units).
- Deck plating was modeled with shell elements to perform DNV RP-C201 Plate/Stiffener Buckling with SDC Verifier.
- Specific structural details, such as module supports, were modeled with shell elements.
- Unit load cases in ANSYS were combined and multiplied with load factors using the Load Combinations functionality of SDC Verifier.
- Unit load cases made it easy to verify the load application and avoid mistakes.
- The number of unit load cases was approximately 50.
- The number of load combinations to address all different design conditions: ULS, blast, accident heel, and fatigue was about 300.
- Since the weight was significantly increased (from 500t to 630t), Bluewater Energy Services B.V. used many load combinations to avoid conservatism and ensure precise results.
- The engineering team used SDC Verifier to create the load combinations according to LRFD and WSD approaches.
- LRFD approach was used for strength and fatigue.
- WSD approach was used for the vessel part: underdeck weld checks, etc.
- In combination with SDC Verifier, Ansys Workbench made sub-modeling easily accessible to address local details for fatigue.
SDC Verifier features and modules allowed to ensure P20 Module safety and serviceability in various operational modes.