The Best Free FEA Software for Fatigue Analysis: A Comprehensive Guide
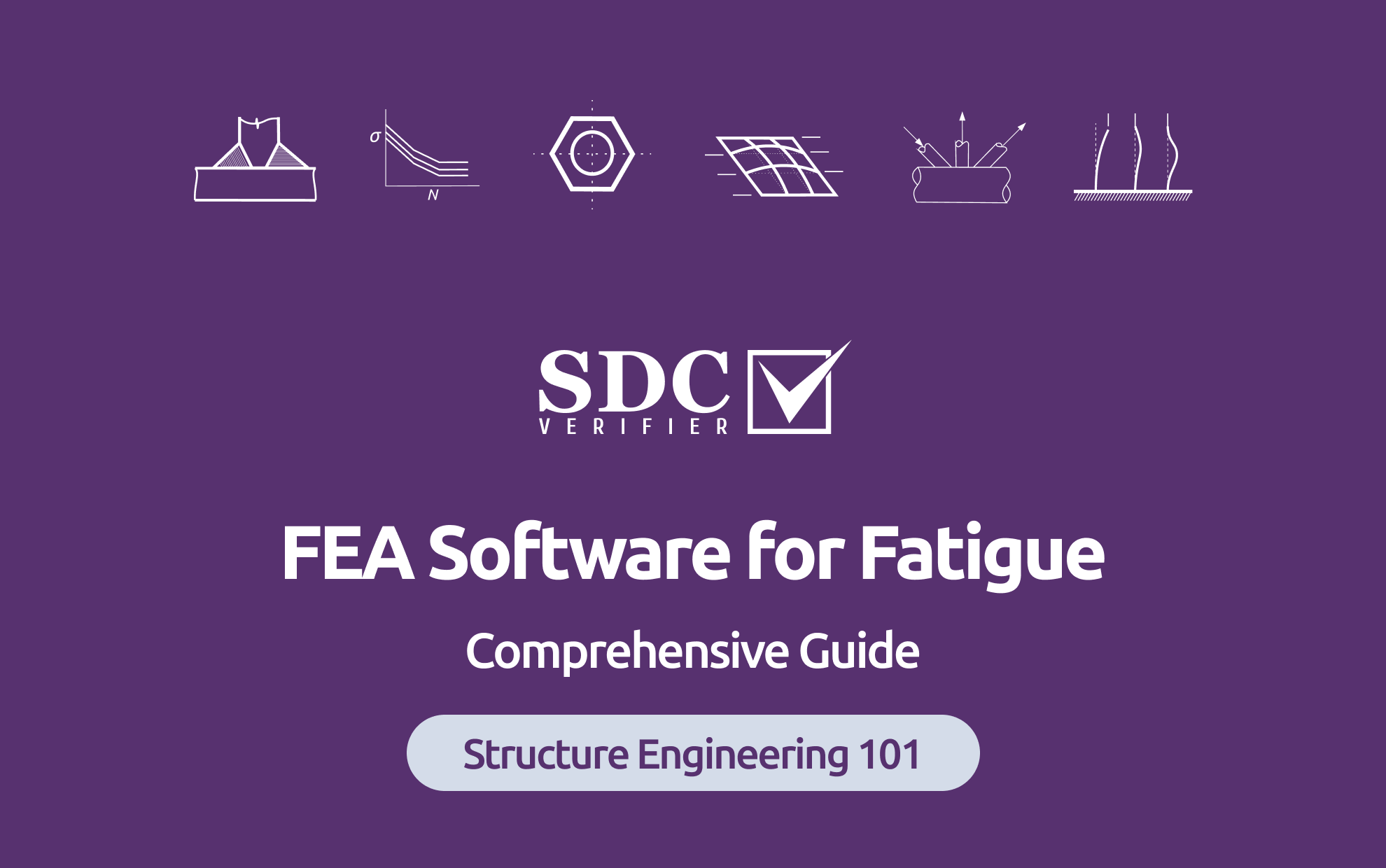
After covering the basics of fatigue and different analysis methods in earlier posts, we’ll now look at tools that simplify this complex process, focusing on the best free FEA software available for fatigue analysis.
These tools are crucial for predicting fatigue life and preventing structural failures, helping engineers create safer and more reliable designs even on a budget.
Read our previous topics in our Fundamentals of Fatigue article series:
- What is Fatigue? (Definitions, Types, Causes)
- Fatigue Strength and Limit (Materials-Specific Data)
- Fatigue Life: Key Influencing Factors and Advanced Prediction Methods
- Fatigue Stress and Its Role in Structural Failure
- How to Calculate Fatigue Strength (Hand Calculations)
- Rainflow Counting Approach
- Fatigue Standards: Essential Guide for Engineers
Why Use FEA Software for Fatigue Analysis?
Fatigue software offers significant advantages over traditional hand calculations, making it a valuable tool for engineers engaged in fatigue analysis.
Accuracy and Complexity Handling
One of the primary benefits of fatigue analysis software is its ability to provide highly accurate predictions. FEA software uses numerical methods to simulate material behavior under cyclic loading, accounting for stress concentrations, material nonlinearity, and multi-axial loading conditions for more realistic and reliable results. For example, in scenarios like predicting lateral torsional buckling, FEA can model the structure’s behavior more accurately than empirical methods, helping engineers prevent premature failure.
Visualization and Insight
Another advantage of fatigue software is its powerful visualization capabilities. Engineers can visualize stress distributions, deformation patterns, and potential failure points, providing deeper insights into the structure’s performance. This is particularly beneficial in complex instances like seismic analysis, where FEA can simulate the gradual formation of plastic hinges in a bridge pier, helping to design safer structures that can withstand extreme events.
Design Optimization and Efficiency
Fatigue analysis software also excels in design optimization. It enables engineers to quickly analyze and compare multiple design options, making identifying the most efficient and cost-effective solution easier. For instance, when designing a footbridge, the best fatigue analysis software can rapidly evaluate configurations, such as truss versus plate girder designs, considering various load conditions and construction stages.
Key Features to Look for in Fatigue Analysis Software
Here are the key features to look for when selecting FEA software for fatigue analysis:
- Material Modeling Capabilities: Supports accurate simulation of different materials’ fatigue properties and cyclic behavior.
- Loading and Boundary Condition Options: Handles variable amplitude loading and multiaxial fatigue to reflect real-world scenarios.
- Meshing and Discretization Tools: Provides flexible and detailed meshing for precise analysis, especially in high-stress areas.
- Solver Capabilities: Includes linear and nonlinear analysis with advanced fatigue life prediction algorithms.
- Post-Processing and Visualization: Offers tools like stress/strain contours and fatigue life plots for clear result interpretation.
- Customization and Scripting: Allows task automation and customization to improve efficiency.
- User Interface and Ease of Use: Features an intuitive, user-friendly interface for streamlined workflows.
- Integration with CAD/Simulation Tools: Ensures smooth data transfer and compatibility with other engineering tools.
Top Free FEA Software for Fatigue Analysis
Various software tools are available for FEA, each offering distinct capabilities suited to different applications. Let’s take a look at some of the best free options:
SDC Verifier
While not entirely free, SDC Verifier offers a free trial, allowing engineers to experience its powerful features for fatigue analysis and design verification. Key benefits include:
- Seamless integration with Ansys, Femap, and Simcenter 3D
- Automation of routine tasks, improving efficiency
- Extensive library of industry standards for compliance
- Parametric modeling for design optimization
- Detailed post-processing and customizable reporting
Ansys Student
Ansys is a leading FEA software known for its robust structural analysis capabilities, including fatigue analysis. The student version offers a limited but powerful subset of features, making it ideal for learning and academic projects.
Altair HyperWorks Student Edition
Altair HyperWorks offers a comprehensive suite for fatigue analysis. Its HyperLife module provides tools for predicting fatigue life under complex loading conditions. The student edition provides access to core functionalities, perfect for students and those starting their FEA journey.
SimScale Community Plan
SimScale is a cloud-based FEA platform that offers a free community plan with limited core hours and storage. While not as feature-rich as the paid plans, it’s an excellent option for trying out cloud-based FEA and performing basic fatigue analysis.
FreeCAD
FreeCAD is a general-purpose parametric 3D CAD modeler that also includes basic FEA capabilities. While not as specialized as dedicated FEA software, it’s a great starting point for simple fatigue analysis and design exploration.
Code_Aster is an open-source FEA software developed by EDF (Électricité de France). It’s a powerful tool with advanced capabilities, but it has a steeper learning curve compared to other options on this list.
Factors to Consider When Choosing Free FEA Software for Fatigue Analysis
Factor | Scenario | Recommended Software |
Complexity of the Analysis | Simple to Moderate Analysis | FreeCAD, SimScale Community Plan |
Complex Analysis | SDC Verifier, Ansys Student, Code_Aster | |
Industry-Specific Requirements | Learning and Academic Projects | Ansys Student, Altair HyperWorks Student Edition |
General Engineering | SDC Verifier, FreeCAD, SimScale Community Plan | |
Team Expertise and Learning Curve | Ease of Use (beginners) | SimScale Community Plan, FreeCAD |
Advanced Users | SDC Verifier, Code_Aster | |
Integration Capabilities | Standalone or Flexible Integration | SDC Verifier |
CAD Integration | Consider options with seamless CAD integration |
Best Practices for Using FEA Software in Fatigue Analysis
1. Importance of Accurate Material Data and Boundary Conditions
- Material Data: Ensure that the material properties you input into the FEA software are as accurate and representative of the actual material as possible. This includes the material’s fatigue properties, such as S-N curves or strain-life parameters. Using generic or incorrect material data can lead to inaccurate fatigue life predictions.
- Boundary Conditions: Properly defining boundary conditions is crucial for realistic simulations. This includes constraints, loads, and interactions that mimic real-world operating conditions. Misrepresenting these factors can cause significant errors in stress distribution, leading to incorrect fatigue assessments.
2. Validation and Verification of FEA Results
- Model Validation: Always validate your FEA model against experimental or benchmark data. This ensures that the model behaves as expected under known conditions. If discrepancies arise, refine your model to capture the physical phenomena better.
- Result Verification: Cross-check FEA results with different analysis methods or software when possible. This helps confirm that the results are not artifacts of a specific solver or mesh setup. Also, mesh sensitivity analysis should be performed to ensure that the results are not dependent on the mesh size.
3. Using Engineering Judgment in Interpreting Results
- Critical Evaluation: FEA results should be interpreted with a strong understanding of engineering principles. The software provides numerical data, but an experienced engineer must assess its significance and implications.
- Safety Factors and Assumptions: Consider your analysis’s safety factors and assumptions. The FEA model may not capture every nuance of the real-world scenario, so applying conservative safety factors and understanding the limits of your assumptions is essential for reliable fatigue analysis.
- Post-Processing: Pay attention to the post-processing stage, where results like stress ranges and fatigue damage are interpreted. Ensure the stress concentrations, potential crack initiation points, and other critical areas are thoroughly evaluated.
Conclusion
Remember that while free FEA software offers valuable capabilities, it might have limitations compared to commercial options. Consider your project’s complexity and requirements when choosing the right tool.
Visit the SDC Verifier website for more detailed information on fatigue analysis and advanced software solutions. Stay updated with the latest insights by subscribing to our blog or request a free consultation or demo to explore how SDC Verifier can enhance your fatigue analysis workflows.