The Fundamentals of Mesh Quality: Why It Matters
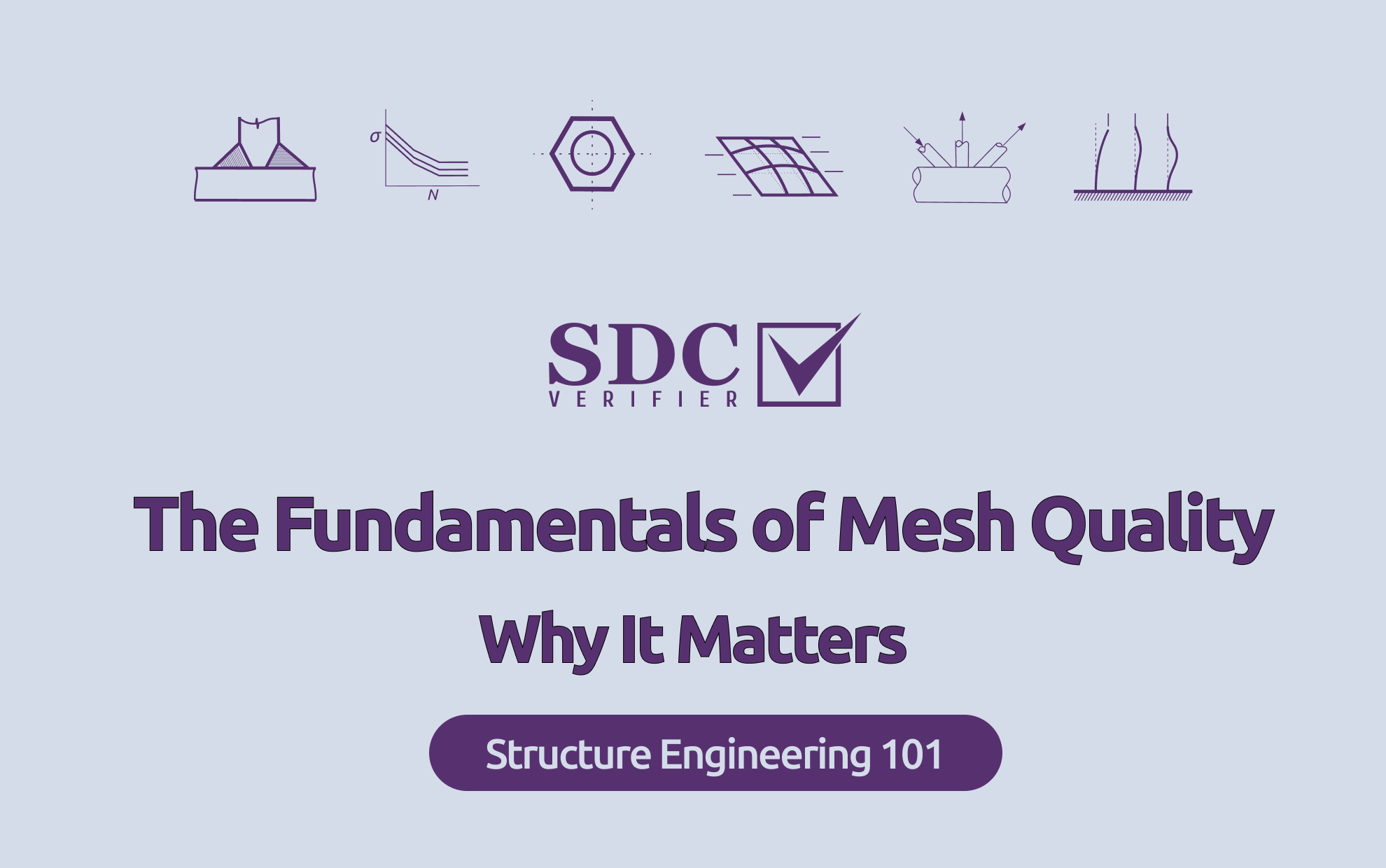
In finite element analysis (FEA), the accuracy and reliability of your results often hinge on one critical factor: mesh quality. A well-constructed mesh is an important factor in ensuring simulations run smoothly and deliver reliable results.
Conversely, a poorly designed mesh can lead to inaccurate predictions, unnecessary computational costs, and overlooked design flaws. This article explores the fundamentals of mesh quality, why it’s essential for FEA, and how engineers can achieve optimal results.
What is Mesh Quality?
Mesh quality in FEA refers to measuring how well a mesh represents a model’s geometry and how effectively it supports accurate and stable finite element analysis (FEA). In simpler terms, it’s an evaluation of the shape, size, and distribution of the mesh elements within a simulation model. A high-quality mesh ensures that the simulation accurately mimics the real-world behavior of the system being analyzed.
Definition of a Mesh in FEA
A mesh in finite element structural analysis is a network of discrete elements and nodes that breaks down a complex geometry into smaller, manageable parts for numerical analysis. Depending on the software and the specific application, these elements can be in various shapes, such as triangles, quadrilaterals, tetrahedrons, or hexahedrons. The mesh is the foundation for solving mathematical equations related to structural, thermal, or fluid dynamics problems.
Key Characteristics of a High-Quality Mesh
- Uniform Element Distribution: While uniform element distribution can help maintain consistency in stress and strain calculations, areas with stress concentrations, sharp corners, or large gradients require finer elements to accurately capture local effects. A well-refined mesh balances uniformity with localized refinement for better accuracy.
- Optimal Aspect Ratios: While elements with aspect ratios close to 1 (square for 2D or cubic for 3D) are generally preferred to minimize numerical errors, the optimal ratio depends on the specific application.
For instance, thin-wall structures or boundary layers may require high aspect ratio elements to align with geometry, and sometimes compromises must be made to reduce the total number of elements, especially in complex geometries.
- Smooth Transitions: Gradual changes in element size are preferred over abrupt transitions to maintain accuracy.
- Accurate Geometry Representation: The mesh must capture complex geometrical details without excessive refinement.
Why Mesh Quality Matters in FEA?
Mesh quality in FEA plays a pivotal role in the success of analysis. It directly impacts the reliability of simulation results, the computational resources required, and the stability of the analysis process. A poor-quality mesh can lead to inaccurate predictions, convergence issues, and inefficiencies, compromising the design and analysis workflow.
Impact on Simulation Accuracy
The primary goal of FEA is to approximate real-world behavior through simulations. A high-quality mesh ensures that the model closely represents the actual geometry and behavior of the analyzed system. Poor-quality meshes, such as those with distorted or irregular elements, can introduce errors, leading to inaccurate stress, strain, or deformation predictions.
Effect on Computational Efficiency
Mesh quality significantly influences the time and resources required to complete a simulation. Poorly constructed meshes with excessively refined or irregular elements can lead to unnecessary computational load, slowing down simulations without improving accuracy. Conversely, a well-designed mesh balances detail with efficiency, optimizing the trade-off between accuracy and computation time.
Influence on Convergence and Stability
Mesh quality affects how smoothly and reliably the numerical solver can complete the analysis. High-quality meshes promote better convergence, reducing the likelihood of errors or non-convergent solutions. Low-quality meshes, on the other hand, often result in instability or divergence, requiring additional iterations and adjustments to resolve.
Watch this video on Mesh Quality in FEA:
Common Mesh Quality Metrics
Engineers rely on specific metrics, to evaluate the quality of a mesh. These metrics assess the geometry, alignment, and performance of individual elements and help identify areas of the mesh that may need refinement or adjustment to ensure accurate and efficient finite element analysis (FEA).
Element Aspect Ratio
The aspect ratio is a measure of the proportionality of an element’s dimensions. For 2D elements, it is typically calculated as the ratio of the longest edge to the shortest edge. In 3D elements, the aspect ratio considers the ratio of element lengths along different axes, making it more complex. Extreme aspect ratios, whether in 2D or 3D, can degrade element performance and accuracy, leading to numerical issues.
- Ideal Range: An aspect ratio < 5 is optimal, as it indicates that the element is nearly square (2D) or cubic (3D).
- Impact of Poor Ratios: Elements with high aspect ratios (e.g., elongated or stretched shapes) can lead to numerical errors and inaccuracies, especially in stress and strain calculations.
Jacobian and Distortion
The Jacobian matrix evaluates the mapping of the element from its natural (idealized) coordinates to the actual coordinates in the mesh.
- Ideal Range: While a Jacobian value close to 1 is generally ideal, acceptable values can vary depending on the solver and analysis type. For some applications, values below 0.6 may still be acceptable.
- Impact of Distortion: Significant deviations in the Jacobian suggest that the element is highly distorted, which can compromise the accuracy and stability of the analysis. Some FEA tools flag elements with poor Jacobian values for correction.
Skewness and Warping
Skewness measures the deviation of an element’s shape from an ideal, symmetrical configuration, while warping assesses the curvature of the element’s faces. It should be 0-0.75 in FEA.
- Skewness: Skewness is typically measured by the deviation of an element’s angles from ideal values (e.g., 90° for quadrilateral elements). High skewness can lead to interpolation errors and uneven stress distributions, as distorted angles introduce higher numerical errors.
The impact of skewness may vary depending on the element type, such as quads versus triangles, with more significant effects on interpolation accuracy in highly skewed elements.
- Warping: Warped elements, where nodes do not lie in the same plane, primarily affect 2D shell elements and can lead to inaccuracies in stress interpolation, especially in thin-shell analyses. Warping is generally not a concern for solid 3D elements, as they do not rely on the same planar node configuration.
- Ideal Range: Elements with low skewness and minimal warping are preferred for accurate simulations.
Node Connectivity and Element Shape
Node connectivity refers to how elements share nodes and edges, while element shape evaluates the regularity of an element’s form.
- Good Connectivity: Properly connected nodes and elements reduce gaps or overlaps, ensuring continuity in the model.
- Element Shape: Well-shaped elements (e.g., equilateral triangles or quadrilaterals for 2D and regular tetrahedrons or hexahedrons for 3D) minimize errors during solution calculations.
Orthogonal Quality
The orthogonal quality measure evaluates how well the angles between mesh elements and their adjacent surfaces align with ideal geometric norms.
- Ideal Value: A perfect orthogonal quality score of 0.2-1, indicates that elements are perpendicular to their neighbors or boundaries.
- Impact of Poor Orthogonality: Misaligned elements lead to numerical inaccuracies, especially in regions with sharp gradients or complex flow paths.
Challenges in Achieving High-Quality Meshes
Creating a high-quality mesh for finite element analysis (FEA) can be a complex task due to the interplay of various factors, including geometry complexity, computational constraints, and the specific requirements of the simulation. Understanding these challenges is key to overcoming them and producing a mesh that balances accuracy and efficiency.
Complex Geometries and Constraints
- Intricate Shapes: Models with detailed or irregular geometries, such as sharp edges, thin walls, or curved surfaces, can be difficult to mesh accurately. These areas often require finer elements to capture details, leading to localized refinement.
- Boundary Conditions: Applying boundary conditions or constraints can affect mesh quality. Sharp changes in boundaries may lead to distorted elements, impacting accuracy in those regions.
- Intersections and Gaps: Overlapping parts, small gaps, or mismatched surfaces in assemblies create challenges for meshing software, often requiring manual correction.
Balancing Accuracy and Computational Cost
- Trade-offs: High-resolution meshes with fine elements improve accuracy but increase computational requirements, leading to longer simulation times. Conversely, coarse meshes reduce computation time but risk compromising the results.
- Mesh Size Limitations: Large-scale models with millions of elements can strain hardware resources, requiring optimization strategies to balance detail and performance.
Handling Large-Scale Models
- Scale Complexity: Engineering models, such as bridges or large machinery, often involve multiple components with varying scales. Maintaining mesh quality across these scales without excessive refinement can be difficult.
- Integration Issues: Combining meshes from different parts or software tools can result in inconsistencies, such as non-matching nodes or uneven transitions.
Software Limitations and User Expertise
- Tool Constraints: Some FEA tools may lack advanced algorithms or adaptive meshing capabilities, requiring manual intervention.
- Learning Curve: Creating high-quality meshes requires experience and a deep understanding of meshing principles, especially for challenging geometries or specialized applications.
Tips for Improving Mesh Quality
Improving mesh quality is essential for ensuring accurate and efficient finite element analysis (FEA). By applying best practices and utilizing advanced meshing tools, engineers can create meshes that balance precision, stability, and computational efficiency. Here are some actionable tips for achieving high-quality meshes:
Best Practices for Mesh Generation
- Start with Clean Geometry: Before generating the mesh, ensure the model is free of unnecessary details, gaps, overlaps, or intersecting surfaces. Clean geometry reduces the likelihood of distorted or ill-defined elements.
- Simplify Where Possible: Remove features not critical to analysis, such as t mall holes which mush less then mesh size used in the whole model, to avoid excessive refinement in those areas.
- Use Symmetry: For symmetrical models, mesh only a portion of the geometry and apply symmetry boundary conditions, reducing computation time while maintaining accuracy.
Advanced Techniques and Tools
- Hexahedral Elements for Critical Applications: Where possible, use structured meshes with hexahedral elements, as they generally offer better accuracy and efficiency compared to unstructured tetrahedral meshes. However, creating hexahedral meshes for complex or curved geometries can be challenging and time-consuming. In such cases, the trade-off between mesh quality and meshing effort should be considered.
- Check and Repair Mesh Quality: Use FEA software’s built-in quality checkers to identify and correct issues such as skewness, aspect ratio, or distorted elements.
-
Use Smoothing and Optimization Tools: Most meshing software includes options for smoothing or optimizing the mesh. These tools adjust node positions to improve element shapes without altering the geometry.
Structural verification software, as SDC Verifier, has instruments to create mesh nodes and elements from geometry and nodes and elements. Regularly validating the mesh against simulation requirements helps maintain accuracy and reliability throughout the analysis.
Using Adaptive Meshing Techniques
- Refine Critical Areas: Focus refinement on regions with high stress gradients, sharp edges, or other critical features while keeping non-critical areas coarser. This targeted approach improves accuracy without inflating computation time.
Identifying critical areas typically involves examining the stress distribution and geometry to pinpoint locations where finer resolution is needed, while non-critical areas can remain coarser.
- Leverage Automatic Mesh Refinement: Many FEA tools offer adaptive meshing algorithms that refine the mesh based on error estimates from preliminary simulations. Use these features to iteratively improve mesh quality.
Leveraging Mesh Refinement in Critical Areas
- Transition Gradually: Ensure smooth transitions between coarse and fine elements to prevent abrupt changes that can lead to inaccuracies. Gradual transitions maintain numerical stability.
- Apply Boundary Layer Meshes: For simulations involving fluid flow, boundary layer meshing is essential to capture gradients near surfaces more effectively. For thin-wall structural problems, however, shell elements are typically more appropriate, as they better represent the geometry and behavior of thin-walled structures.
Advanced Techniques and Tools
- Hexahedral Elements for Critical Applications: Where possible, use structured meshes with hexahedral elements, as they generally offer better accuracy and efficiency compared to unstructured tetrahedral meshes.
However, creating hexahedral meshes for complex or curved geometries can be challenging and time-consuming. In such cases, the trade-off between mesh quality and meshing effort should be considered.
2. Check and Repair Mesh Quality: Use FEA software’s built-in quality checkers to identify and correct issues such as skewness, aspect ratio, or distorted elements.
3. Use Smoothing and Optimization Tools: Most meshing software includes options for smoothing or optimizing the mesh. These tools adjust node positions to improve element shapes without altering the geometry.
Structural verification software, as SDC Verifier, has instruments to create mesh nodes and elements from geometry and nodes and elements. Regularly validating the mesh against simulation requirements helps maintain accuracy and reliability throughout the analysis.
Conclusion
Mesh quality is the backbone of successful finite element analysis, directly influencing the accuracy, efficiency, and reliability of simulations. By understanding the fundamentals, applying best practices, and leveraging advanced tools like those in structural verification software, engineers can ensure their meshes are well-optimized for real-world applications. Whether it’s improving geometry representation, refining critical areas, or maintaining computational efficiency, a high-quality mesh lays the foundation for dependable and insightful analysis results.