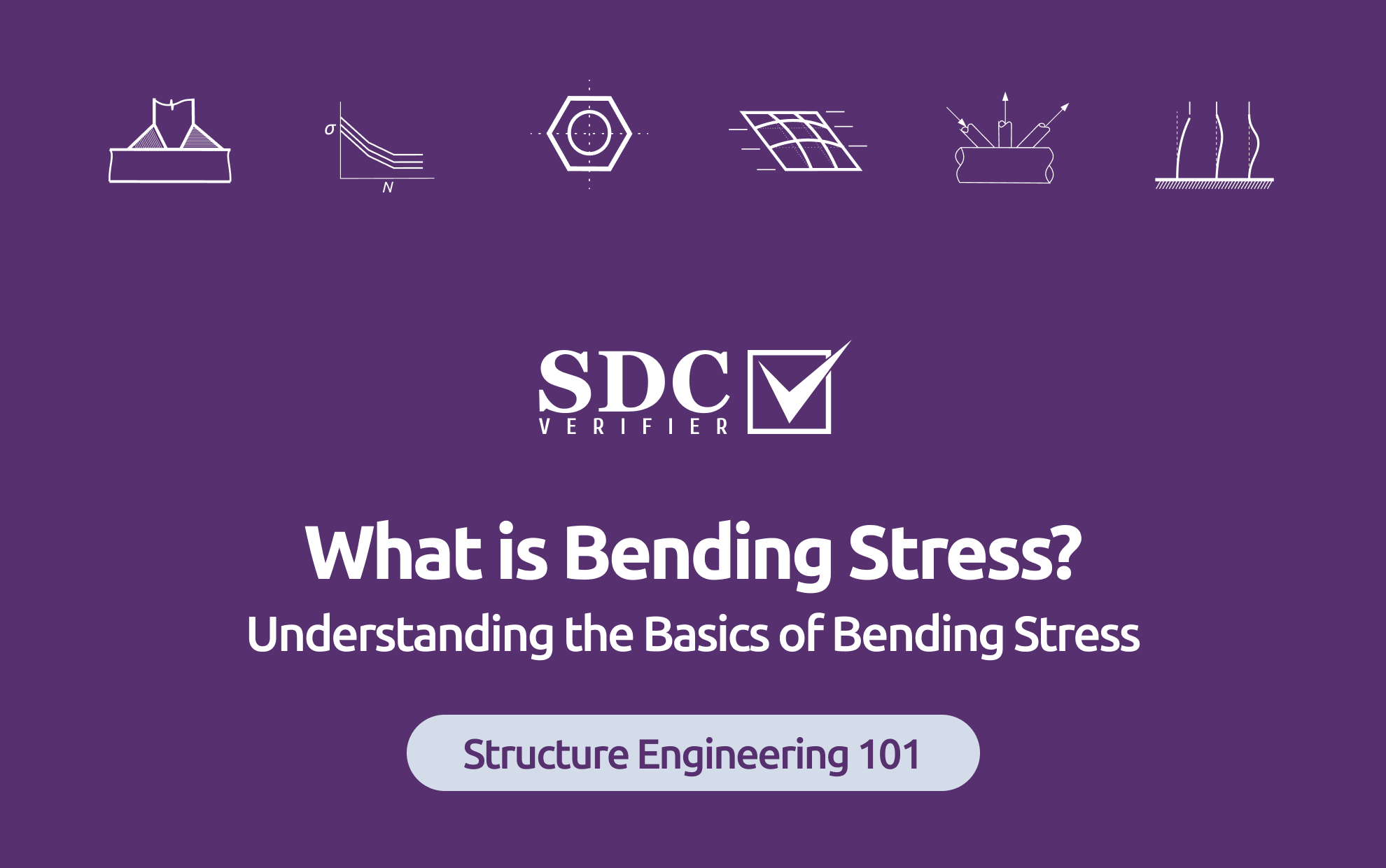
Bending stress, also known as flexural stress or simply bending, occurs when an object is subjected to external forces that cause it to bend or deform. In engineering, understanding and analyzing this phenomenon significantly impacts designing and evaluating the structural integrity of various components.
Understanding the Basics of Bending Stress
Before exploring this phenomenon, it’s crucial to establish a clear definition and recognize its significance. Bending stress is the internal strain that develops within a material when it undergoes deformation due to the applied bending moment. As materials are subjected to external loads, such as forces or moments, their resistance to bending can significantly impact their structural performance.
Understanding bending load is crucial in various engineering disciplines, including civil, mechanical, and aerospace engineering. Engineers must consider it when designing structures such as bridges, beams, and aircraft wings to ensure the safety and reliability of these critical components. By analyzing the strain caused by bending, engineers can determine the maximum load a structure can withstand before failure, allowing them to make informed design decisions.
Factors Influencing Bending Stress
Several factors influence the magnitude and distribution of bending load within a material. Firstly, the material’s mechanical properties, including its modulus of elasticity, yield strength, and flexibility, can significantly affect the generated stress. Secondly, the shape and dimensions of the object subjected to bending are essential. Objects with larger cross-sectional areas and increased moment of inertia are capable of withstanding higher flexural strains.
Furthermore, the type of loading applied to a material can also impact the deformation load. Different loading conditions, such as cantilevered beams, supported beams, or overhanging beams, result in varying stress distributions along the length of the material. Engineers must carefully analyze the loading scenario to forecast and reduce potential failure due to flexural force. Additionally, environmental factors such as temperature variations and corrosion can further influence the behavior of materials under bending, emphasizing the need for comprehensive stress analysis in real-life scenarios.
The Science Behind Bending Stress
Material properties directly affect the behavior of stress caused by bending. For instance, the modulus of elasticity determines how much a material will deform under a given load. Materials with higher modulus values exhibit greater stiffness and are less prone to deformation. Conversely, materials with lower modulus values are more flexible and susceptible to significant bending. Yield strength, alternatively, represents the maximum stress a material can withstand without permanent deformation, making it a critical characteristic for the structural design process.
The ultimate tensile strength is another critical material property in the strain experienced during bending. This parameter signifies the maximum stress a material can endure before fracturing. Understanding the interplay between yield strength and ultimate tensile strength is essential for ensuring the structural integrity of components subject to flexural load. Moreover, a material’s flexibility, which refers to its ability to deform plastically before fracturing, impacts how it responds to bending forces. Materials with higher ductility can undergo more significant deformation before failure.
Bending Stress Equations and Calculations
Engineers use mathematical equations and calculations to analyze and accurately predict the strain caused by loading. The most common formula employed is the flexure formula, also known as the bending equation, which relates the applied moment, the material’s flexural modulus, and the object’s geometry. By solving the flexural equation, engineers can assess the maximum stress at any point along the object and identify potential failure points.
Different Types of Bending Stress
Understanding the behavior of materials under different types of structural stress and finding out how forces interact with structural elements is important. Pure flexural strain, for instance, is a fundamental concept in mechanics that demonstrates the symmetry of loading and deflection in objects like beams and columns. The uniform distribution of forces in pure bending load leads to predictable deformation patterns, which is essential in designing and analyzing various structures.
However, the real-world application of curvature-induced stress is only sometimes as straightforward as pure bending. Transverse flexural strain adds complexity by causing non-uniform deformation in materials, resulting in varying loading and deflection levels along an object’s length. This type of bending stress is highly important in scenarios where external forces are not evenly distributed, such as in beams with point loads or structures experiencing eccentric loading conditions. Engineers and designers need to closely evaluate transverse deformation strain to predict the behavior of materials and ensure structural integrity accurately.
Pure Bending Stress
It occurs when an object experiences uniform deformation along its length, resulting in symmetric loading and deflection. We can often observe this type of stress in beams, columns, or other structural elements subjected to simple loads. Understanding how pure curvature-induced stress affects different materials and configurations is essential for ensuring these structures’ safe and efficient performance.
Transverse Bending Stress
This type of deformation usually occurs when an object experiences non-uniform bending, leading to uneven loading and deflection. We can commonly see it in situations where the applied bending moment varies across the length of the material, such as beams with concentrated loads or objects under eccentric loading conditions. Correctly accounting for transverse flexural force is vital for accurate structural analysis and design.
Measuring Bending Stress
Tools and Techniques for Measuring Bending Stress
Precisely measuring stress from bending forces is essential for evaluating the structural integrity of components. Several tools and techniques exist for this task, including strain gauges, load cells, extensometers, and finite element analysis (FEA) software. These tools allow engineers to quantify the distribution and magnitude of deformation load within a material or structure, helping assess its mechanical performance.
Strain gauges are commonly used to measure flexural force by detecting the deformation of a material under load. By analyzing the strain, engineers can calculate the stress experienced by the material due to bending forces. Load cells, instead, directly measure the applied force on a structure, determining the loading force based on the material properties.
Interpreting Bending Stress Results
Once flexural strain measurements are obtained, it is essential to interpret and analyze the results effectively. Engineers must consider safety factors, material limits, and design specifications to reach informed conclusions regarding the structural integrity and performance of the analyzed object. Proper interpretation of bending load results allows for optimizing designs and identifying potential areas of improvement.
Furthermore, finite element analysis (FEA) software mainly predicts the deformation strain distribution in complex structures. By dividing the structure into more minor elements and analyzing their interactions, FEA software can explain the behavior of materials under bending loads. This computational tool is important for simulating real-world conditions and optimizing designs for maximum performance and safety.
Mitigating Bending Stress
Design Considerations to Reduce Bending Stress
Reducing flexural stress is often a primary goal in the design process. Engineers optimize the object’s shape, dimensions, and material selection to ease the strain experienced during loading. By making proper design choices, such as using materials with higher modulus values, incorporating additional supports, or changing the object’s cross-sectional shape, engineers can significantly reduce curvature-induced force and boost the structure’s performance.
An important design factor for reducing flexural load is selecting materials with higher modulus values. A material’s modulus means its stiffness or ability to resist deformation under stress. By selecting materials with higher modulus values, engineers can guarantee the object can withstand external forces without experiencing excessive structural force. For instance, engineers often use high-strength steel or reinforced concrete with high modulus values to minimize flexural load and ensure the bridge’s structural integrity.
Apart from material selection, incorporating additional supports can also reduce strain caused by bending. By strategically placing supports along the object’s length, engineers can distribute the load more evenly, lowering the amount of flexural force at specific points. To illustrate, engineers often have intermediate supports to prevent excessive loading at the free end in the design of cantilever beams. These supports provide resistance, reducing the bending moment and deformation experienced by the beam.
Maintenance Practices to Manage Bending Stress
Even after the first design steps, monitoring and managing flexural load is vital for the continued operation and safety of components and structures. Regular maintenance practices, including inspections, load monitoring, and stress analysis, allow for early detection of potential issues related to structural strain. Through proactive maintenance and repair, engineers can address any vulnerabilities and ensure the longevity and reliability of the object throughout its operational life.
Inspections play a vital role in managing curvature-induced load by identifying signs of deformation, cracks, or fatigue in the structure. By conducting visual inspections and using non-destructive testing techniques, engineers can spot early indicators of flexural stress-related issues and take the proper steps to prevent further damage. Load monitoring is another essential maintenance practice that involves measuring and analyzing the forces and moments acting on the object. By continuously monitoring these loads, engineers can identify any abnormal or excessive structural strain and take corrective actions to prevent failure.
Stress analysis is also a valuable tool in managing deformation load. Engineers can predict and analyze a structure’s distribution of flexural force through computer simulations and mathematical modeling. This analysis helps identify areas of high-stress concentration, allowing engineers to make informed decisions regarding reinforcement or modifications to reduce strain experienced during bending. By regularly performing stress analysis, engineers can manage flexural load proactively and ensure the object’s structural integrity.
Conclusion
So, bending stress is a fundamental concept in engineering, with significant implications for the design, analysis, and maintenance of various structural elements. By understanding its basics, considering the role of material properties, and applying appropriate measurement and mitigation strategies, engineers can ensure the integrity and performance of structures in the face of external forces and moments.