Ensuring Joint Integrity with Bolt Connection Calculations
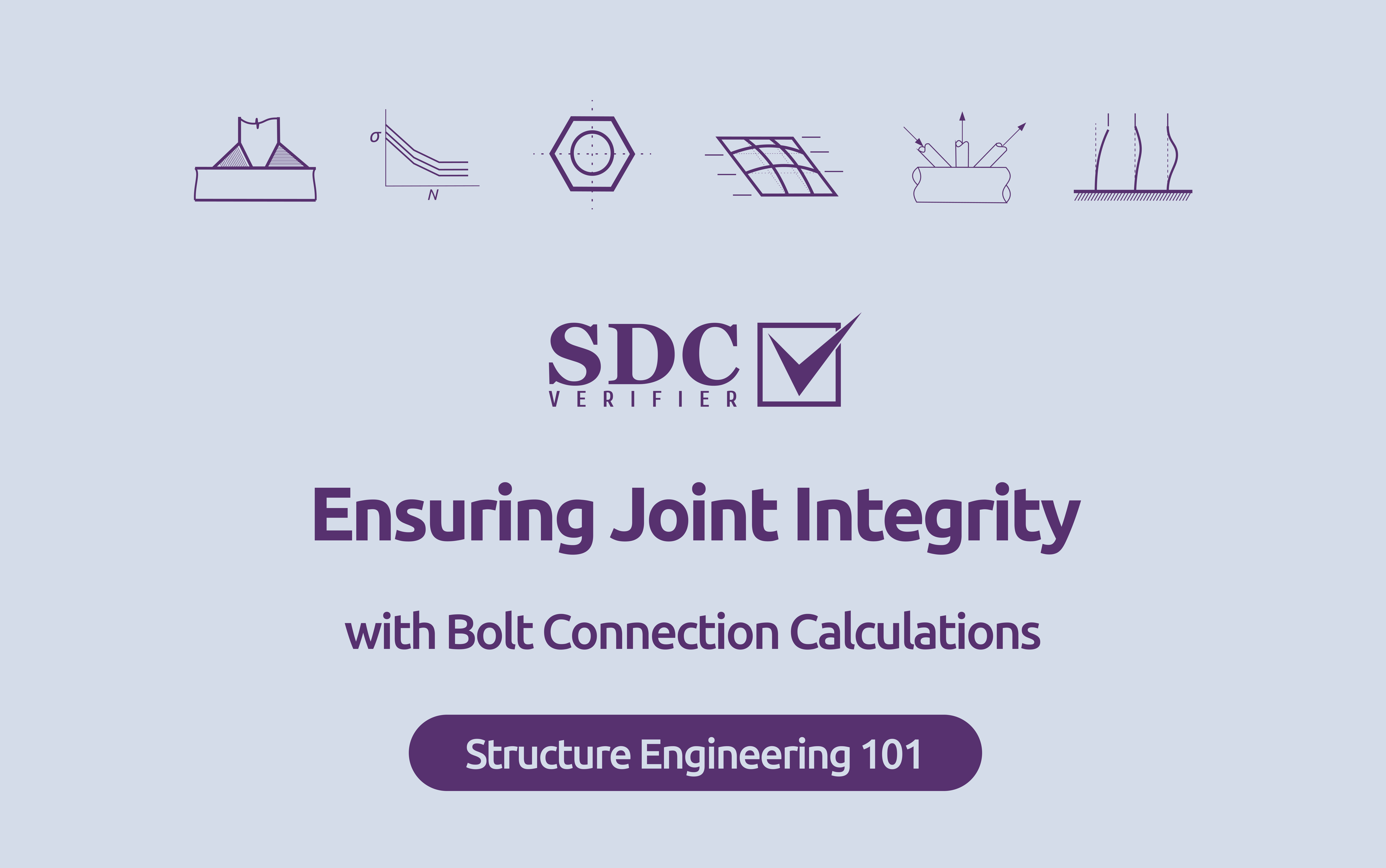
Engineers must evaluate preload, load dynamics, material compatibility, joint stiffness, and stress distribution in designing practical bolted joints. These elements ensure the joint can withstand operational demands and maintain integrity over time.
To ensure the longevity and safety of these connections, engineers must also account for conditions like fluctuating loads, environmental exposure, and fatigue resistance, aligning each design to rigorous reliability standards.
This article discusses the most important elements of bolted joint design, focusing on three key aspects: understanding joint integrity, performing bolt connection calculations, and implementing a robust verification process.
Read our previous articles about bolts:
- Standards for Bolts: A Comprehensive Guide
- Understanding Bolt Specifications: A Beginner’s Guide
- Bolt Strength Calculations: Understanding the Fundamentals
- Bolt Stress Calculations: A Step-by-Step Guide
- Bolt Loading Calculations: Factors to Consider
- Bolt Fatigue Calculations: A Practical Approach to Structural Integrity
What is Joint Integrity?
Ensuring joint integrity is foundational in bolted joint design, as it dictates the ability of a joint to withstand operational stresses, environmental factors, and load variations over time. Joint integrity encompasses a combination of material properties, geometric considerations, and loading conditions that collectively define the reliability and durability of the bolted connection. Engineers focus on stress distribution, preload management, and fatigue resistance to enhance joint integrity in static and dynamic applications.
1. Stress Distribution and Load Paths
Proper stress distribution is nearly impossible in the real world due to factors like bolt spacing, stiffness differences, and joint geometry. However, engineers can reduce stress concentrations by selecting appropriate joint geometries and bolt patterns and ensuring that load paths are efficient and consistent with the design requirements.
For example, each bolt should share the load proportionally in multi-bolt configurations. However, bolt spacing, joint stiffness, and material compatibility can lead to uneven load sharing. Finite Element Analysis (FEA) can provide insight into the distribution of stress within the joint, helping engineers optimize design elements and predict failure points under different loading scenarios.
2. Preload and its Impact on Joint Performance
Proper preload ensures that the joint remains in compression under operational loads, reducing the likelihood of relative movement between joint components and minimizing fatigue. Preload creates a clamping force that counteracts external loads and reduces the bolt’s cyclic stress amplitude, significantly enhancing its fatigue life and maintaining joint integrity.
To control preload, engineers must consider factors like the yield strength of the bolt material, the coefficient of friction between joint surfaces, and the torque applied during installation. However, achieving and maintaining optimal preload can be challenging due to potential losses from relaxation, creep, and thermal effects. Advanced methods for measuring preload include torque-angle methods, ultrasonic measurement, direct tension indicators, and load-indicating washers or strain gauges. These techniques enable precise preload control, crucial in applications where preload loss could compromise joint safety and performance.
(source)
3. Fatigue Resistance and Durability
Fatigue is a primary concern in bolted joints exposed to cyclic or fluctuating loads, as repeated stress can lead to crack initiation and propagation over time. Engineers design bolted connections to maximize fatigue resistance by selecting materials with suitable fatigue properties and managing stress concentrations within the joint.
Additionally, factors such as surface finish, thread design, and residual stresses significantly influence the fatigue behavior of bolted joints, further affecting their long-term performance.
To reduce the risk of fatigue failure, engineers might incorporate undercut bolt heads, optimized thread designs, and filleted bolt shanks, which help alleviate stress concentrations. Filleted bolt shanks help reduce stress concentrations at transitions, while optimized threads ensure a more uniform load distribution along the engaged threads. Both of these contribute to improved fatigue resistance and joint longevity.
Also, selecting materials with high fatigue limits and using protective coatings to prevent corrosion can further enhance fatigue resistance and prolong joint life. Fatigue testing, including S-N curve analysis, provides valuable data to predict the life expectancy of a joint under specific loading conditions.
4. Environmental Factors
Factors such as temperature fluctuations, exposure to corrosive elements, and moisture can all compromise joint integrity. Studies have shown that as steel strength increases, the material becomes increasingly sensitive to stress corrosion and hydrogen-induced stress cracking. This heightened susceptibility requires careful material selection and joint design, especially in environments where these types of degradation could impact structural integrity.
Bolt Connection Calculations
Bolt connection calculations typically involve determining the axial, shear, and combined forces acting on the bolt. These stresses help engineers evaluate the bolt’s capacity and understand whether it can withstand applied loads without failure. Here, we’ll go through some core calculations:
1. Preload Force Calculation
The preload force is the initial tension applied to a bolt, typically during tightening. Proper preload ensures the joint remains tight and can resist external loads without loosening.
The preload force is typically 65-75% of the bolt material’s yield strength, depending on the relevant standard.
For standard metric bolts with ISO thread profiles, the tensile stress area At can be estimated using the nominal diameter d and thread pitch p:
At=0.7854⋅(d−0.9382⋅p)2
Note that this formula applies only to standard threads and may not be suitable for non-standard threads or coarse pitches.
2. Tensile Stress in the Bolt
Tensile stress is generated when an external axial load is applied to the bolt. The tensile stress must remain within safe limits to avoid failure.
σtensile=Fa/At
where:
- σtensile = Tensile stress (Pa)
- Fa = Applied axial force on the bolt (N)
- At = Tensile stress area of the bolt (m²)
3. Shear Stress Calculation
Shear stress occurs when a transverse load is applied to the joint, trying to slide the bolt across the shear plane. For bolted joints, it’s important to verify that shear stresses remain within the bolt’s capacity.
For a single-shear plane:
τ=Fs/As
where:
- τ = Shear stress (Pa)
- Fs = Applied shear force (N)
- As = Cross-sectional shear area of the bolt (m²)
Note that this equation assumes the entire cross-sectional area of the bolt is engaged in shear.
For a double-shear joint (where the bolt experiences shear on two planes):
τ=Fs/2⋅As
4. Combined Stress Analysis: Von Mises Criterion
In many real-world applications, bolts are subjected to axial, and shear loads simultaneously. The Von Mises stress criterion is commonly used to evaluate combined stresses and ensure they don’t exceed the material’s yield strength.
Where:
- σv = Equivalent (Von Mises) stress (Pa)
- σtensile = Axial tensile stress (Pa)
- τ = Shear stress (Pa)
This combined stress calculation ensures that the bolt can safely handle the simultaneous stresses without yielding. However, it is not directly applicable to brittle materials, which typically require different criteria. Additionally, safety factors are often applied alongside the Von Mises criterion to provide an extra margin of safety in design.
5. Bolt Group Load Distribution
When bolts are used in a group (e.g., to join large structures), the applied load must be distributed among the bolts. For an accurate analysis, especially in cases with multiple fasteners, engineers use centroidal moments and shear center location principles to assess load distribution.
For a simple bolt group of two bolts, if an external load FFF acts perpendicular to the line connecting the bolts, the force shared by each bolt is:
Fbolt1=Fbolt2=F/2
Engineers often rely on matrix calculations in more complex bolt configurations, such as stiffness matrices or influence coefficient methods, to analyze load distribution. These methods account for factors like bolt stiffness and joint geometry to represent load sharing accurately. For even greater precision, finite element analysis (FEA) is used to simulate the detailed behavior of the assembly under load.
6. Torque Calculation for Preloading
A specific torque is applied to the bolt to achieve the desired preload. Factors like friction between the threads and the bearing surface affect the relationship between torque and preload.
T=K⋅Fp⋅d
Where:
- T = Applied torque (Nm)
- K = Torque coefficient (dimensionless), typically ranging from 0.2 to 0.3 depending on the lubrication and surface finish
- Fp = Desired preload force (N)
- d = Nominal diameter of the bolt (m)
However, the torque coefficient (KKK) is not constant and can vary significantly based on factors like lubrication, surface finish, and thread contamination. This variability can impact preload accuracy, potentially leading to insufficient or excessive clamping force. Ultrasonic preload measurement or load-indicating devices to mitigate these uncertainties and achieve more precise preload control for critical applications.
Verification Process
1. Verification of Material Properties
Material properties such as axial force, shear force, slip resistance check, and mail compatibility are critical to ensuring that a bolt can withstand applied forces without permanent deformation or failure.
- Axial Force Check (Tension)
The bolt must withstand axial forces without exceeding its yield strength (). This ensures the bolt does not experience plastic deformation under preload and applied loads:
If the bolt fails the yield strength check, further analysis for tensile strength becomes unnecessary, as yielding is the limiting condition.
- Shear Force Check
The bolt’s shear capacity is evaluated to ensure it can resist applied shear forces without failure. Shera stress is calculated and compared to the allowable shear strength of the bolt material:
This check is critical in preventing material failure around the bolt holes.
- Slip Resistance Check (for Preloaded Bolts)
For bolts with prestressing, slip resistance must be evaluated to ensure the joint does not experience relative movement under applied loads. The clamping force from preload and the friction coefficient of the joint surface determine the resistance to slippage.
- Material Compatibility
The materials of the bolt and the connected parts must be compatible to avoid issues like galvanic corrosion, especially in harsh environments. This prevents long-term degradation and preserves joint integrity.
2. Verification Against Standards and Codes
Compliance with relevant design codes and standards is essential for engineering applications to ensure that joints meet industry safety and performance criteria. Standards from organizations like the American Society of Mechanical Engineers (ASME), American Institute of Steel Construction (AISC), and ISO specify guidelines for load capacities, safety margins, and permissible stress limits.
- ASME B18.2.1: Provides specifications for dimensions and tolerances for bolts.
- AISC 360: Covers bolt connections for structural steel and its load-bearing capabilities.
- ISO 898-1: Specifies mechanical properties for fasteners made from carbon and alloy steels.
For this purpose, you can use structural engineering software SDC Verifier, which can accurately provide standard verification for your bolted joint model.
3. Finite Element Analysis (FEA) for Complex Loadings
In cases where bolted joints are subject to complex or dynamic loads, Finite Element Analysis (FEA) provides a more comprehensive verification. FEA simulation allows engineers to visualize stress distribution and deformation across the joint under simulated load conditions.
- Stress Distribution: FEA highlights areas of high stress and potential failure points.
- Dynamic Loading: FEA can simulate fatigue behavior and assess the joint’s endurance over time in cases involving vibration or variable loading.
FEA models are essential for validating that stresses remain below the yield strength. They also evaluate critical factors such as fatigue life, contact pressures, and stress gradients, ensuring that load distributions and other performance criteria stay within allowable limits under realistic operating conditions.
5. Testing for Verification
Physical testing complements theoretical calculations and FEA to verify joint integrity in critical applications. Common verification tests include:
- Torque Testing: Confirms that preload torque aligns with calculations.
- Shear and Tensile Load Testing: Applies axial and transverse loads to confirm that the joint performs within the design’s safety margin.
- Environmental Testing: This involves exposing the joint to specific environmental conditions (e.g., temperature, humidity) to evaluate material compatibility and corrosion resistance.
Testing is particularly valuable when the application demands extreme reliability, such as in aerospace, automotive, or heavy equipment industries.
Conclusion
Bolted connections are essential to the safety and durability of many engineering structures, and ensuring their integrity requires a thorough understanding of joint design, stress management, and verification methods. Engineers can achieve high-performance joints capable of withstanding operational demands by implementing precise bolt connection calculations and a rigorous verification process. These methods prevent premature failures, uphold industry standards and promote long-term reliability.