Fatigue Standards: Essential Guide for Engineers
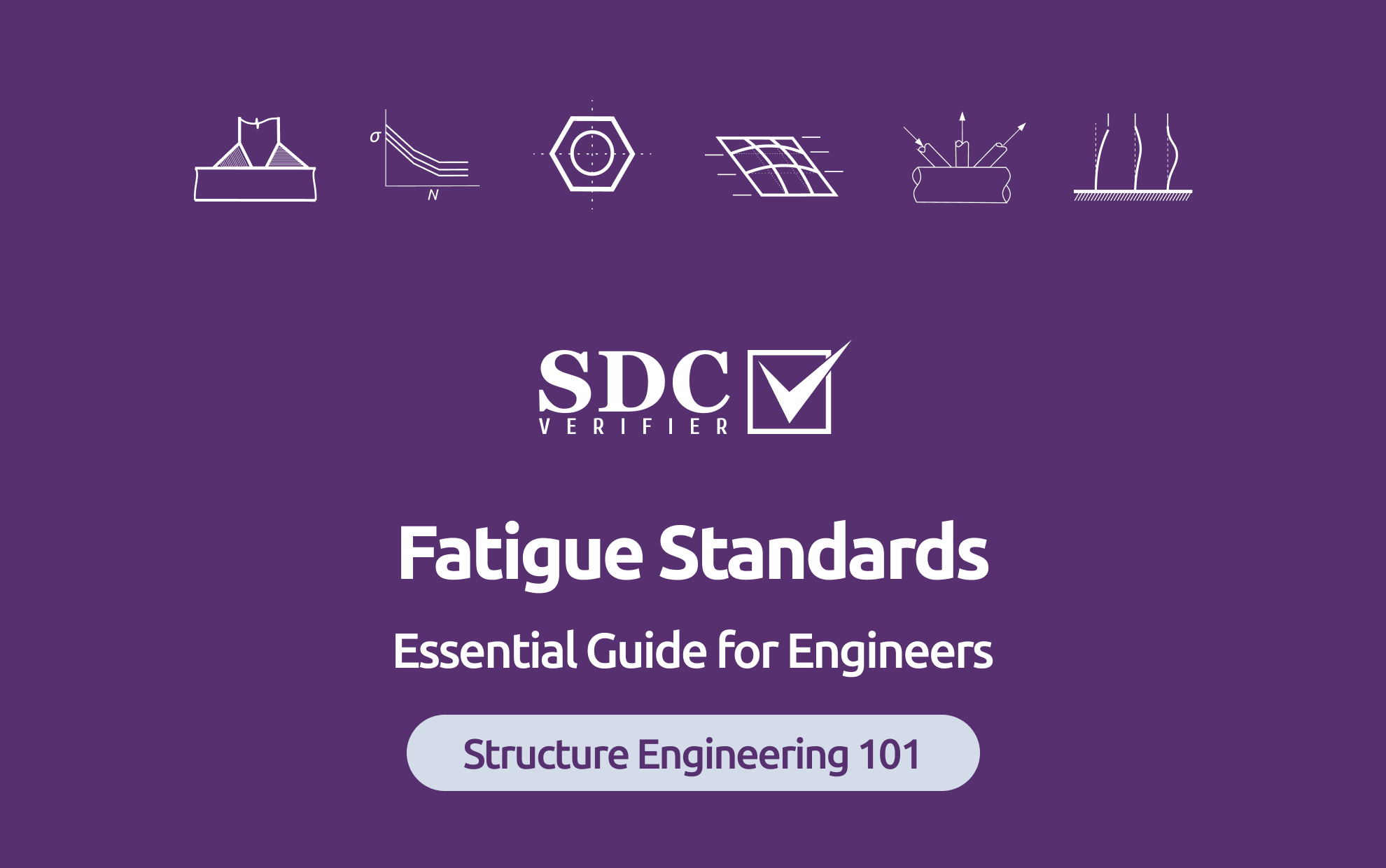
Fatigue standards play a crucial role in addressing fatigue, a critical factor in engineering design that affects the durability and safety of structures. It refers to the progressive and localized structural damage that occurs when a material is subjected to cyclic loading. Over time, even small stresses can lead to the development of cracks, which can propagate and ultimately result in catastrophic failure.
Read our previous topics in our Fundamentals of Fatigue article series:
- What is Fatigue? (Definitions, Types, Causes)
- Fatigue Strength and Limit (Materials-Specific Data)
- Fatigue Life: Key Influencing Factors and Advanced Prediction Methods
- Fatigue Stress and Its Role in Structural Failure
- How to Calculate Fatigue Strength (Hand Calculations)
- Rainflow Counting Approach
Overview of Key Fatigue Standards
Below is a brief summary of the fatigue standards supported by SDC Verifier:
DIN 15018 (1984)
- Scope: Applies to the steel structures of cranes, crane equipment of all types, and mobile steel structures used in continuous conveyors.
- Applications: Strength and fatigue analysis for dynamic loading of cranes and lifting equipment.
- Key Methods: Fatigue assessment based on the loading groups according to stress cycle ranges and stress collectives.
- Considerations: Emphasizes safety margins for cyclic loading in crane design.
DIN DVS 1608 (June 2010)
- Scope: Applies to the aluminum structures in railway applications.
- Applications: Fatigue assessment for welded aluminum joints.
- Key Methods: S-N curves used for assessing the fatigue life of welded components.
- Considerations: Specific to stress concentrations in welded joints.
DIN DVS 1612 (August 2014)
- Scope: Applies to steel structures in rail-vehicle construction.
- Applications: Strength and Fatigue verification of the rail-vehicle construction.
- Key Methods: Utilizes S-N curves and Palmgren-Miner rule.
- Considerations: Addresses weld-specific fatigue damage.
DNV-RP-C203 Fatigue (2016)
- Scope: Offshore structures, oil & gas, and maritime industries.
- Applications: Fatigue life assessment of offshore and maritime components.
- Key Methods: S-N curves, cumulative damage using Palmgren-Miner rule.
- Considerations: Suitable for marine and dynamic environmental loading.
EN13001 (2018)
- Scope: General design of cranes and lifting equipment.
- Applications: Strength and Fatigue assessment in machinery subject to repetitive loads.
- Key Methods: Fatigue analysis is based on S-N curves.
- Considerations: Takes into account cyclic loads and safety factors for machinery.
Eurocode 3 Fatigue (EN1993-1-9, 2005)
- Scope: Steel structures under dynamic loading.
- Applications: Civil engineering, heavy lifting, machinery.
- Key Methods: Fatigue assessment based on load histories and stress ranges.
- Considerations: Comprehensive fatigue analysis for steel structural components.
FEM 1.001 (3rd, 1998)
- Scope: Hoisting appliances and lifting systems.
- Applications: Strength and Fatigue analysis for cranes and hoisting systems.
- Key Methods: Uses S-N curves for fatigue life calculation.
- Considerations: Focus on static and fatigue strength in hoisting machinery.
FKM (5th, 6th Editions)
- Scope: Analytical strength assessment for mechanical components.
- Applications: Industrial machinery, railways, and energy.
- Key Methods: Smith Correction, Palmgren-Miner rule for S-N curve fatigue analysis.
- Considerations: Considers multiple loading patterns and environments.
Utilizing Fatigue Standards in Design and Analysis
Fatigue standards play a critical role in ensuring the safety, reliability, and durability of engineered structures. Engineers must integrate these standards into their design and analysis processes to comply with regulatory requirements and prevent fatigue-related failures. This article explains how engineers can use fatigue standards effectively and offers practical tips on applying fatigue assessment criteria in real-world scenarios.
Importance of Fatigue Standards
Adhering to relevant fatigue standards is essential for:
- Safety: Ensuring structural integrity under cyclic loading conditions.
- Compliance: Meeting industry and legal requirements in various engineering fields.
- Longevity: Extending the operational life of structures by predicting and mitigating fatigue failures.
How Engineers Can Utilize Fatigue Standards
Engineers can integrate fatigue standards throughout the design and analysis phases by following these key steps:
1. Identify Relevant Standards Based on the project, identify the applicable fatigue standards. For example:
- ASME VIII (2010): For pressure vessels and boilers.
- DNV OS-C101 and DNV-RP-C203: For offshore and maritime structures.
- EN 13001: For crane safety and machinery design.
- Eurocode 3 Fatigue: For civil engineering structures.
- FEM 1.001: For hoisting appliances and machinery.
2. Interpret Fatigue Assessment Criteria Fatigue standards outline specific methods for assessing fatigue. For example:
- S-N Curve Analysis: Commonly used in ASME VIII and Eurocode 3, this method helps estimate the number of load cycles a material can endure before failure.
- Palmgren-Miner’s Rule: Often used in FKM standards, this rule accumulates fatigue damage over variable loads to predict fatigue life.
- Rainflow Counting: Utilized for DNV OS-C101 fatigue checks to analyze complex load cycles.
3. Apply Criteria to Real-World Designs Ensure that the fatigue assessment methods are applied to the specific load conditions and materials used in the design. For instance:
- Pressure Vessels: Use ASME VIII standards to ensure safety under high-pressure cycles.
- Offshore Structures: Follow DNV OS-C101 to assess fatigue from wave loads and environmental stressors.
Tips for Applying Fatigue Standards
- Choose the Right Standard: Select fatigue standards based on the application (offshore, civil engineering, machinery) and material behavior under cyclic loading.
- Simulate Loading Conditions: Use Finite Element Analysis (FEA) software to simulate realistic loading conditions and verify fatigue life.
- Regularly Update Compliance: Fatigue standards are periodically updated, so always ensure you are using the latest versions (e.g., ASME VIII Div2 (2010), DNV-RP-C203 (2016)).
- Consider Environmental Factors: Environmental conditions like corrosion and temperature variation can accelerate fatigue. Apply the relevant fatigue check methods, such as those outlined in EN 13001 for machinery and cranes.
Conclusion
Fatigue standards are essential tools for engineers, ensuring that structures remain safe and reliable under cyclic loads. By integrating these standards into design and analysis, engineers can predict fatigue life, prevent potential failures, and meet industry regulations. Whether working with pressure vessels, offshore structures, cranes, or civil engineering projects, understanding and applying the relevant fatigue standards is key to maintaining safety and compliance.
Take the time to explore the specific fatigue standards relevant to your field, such as ASME VIII, DNV-RP-C203, or Eurocode 3 Fatigue, and ensure you’re using the best practices for fatigue assessment. For more details on how these standards apply to different engineering sectors, visit our comprehensive list on the SDC Verifier website.