Empowering Civil Engineering: Mitigating Structural Design Risks with SDC Verifier
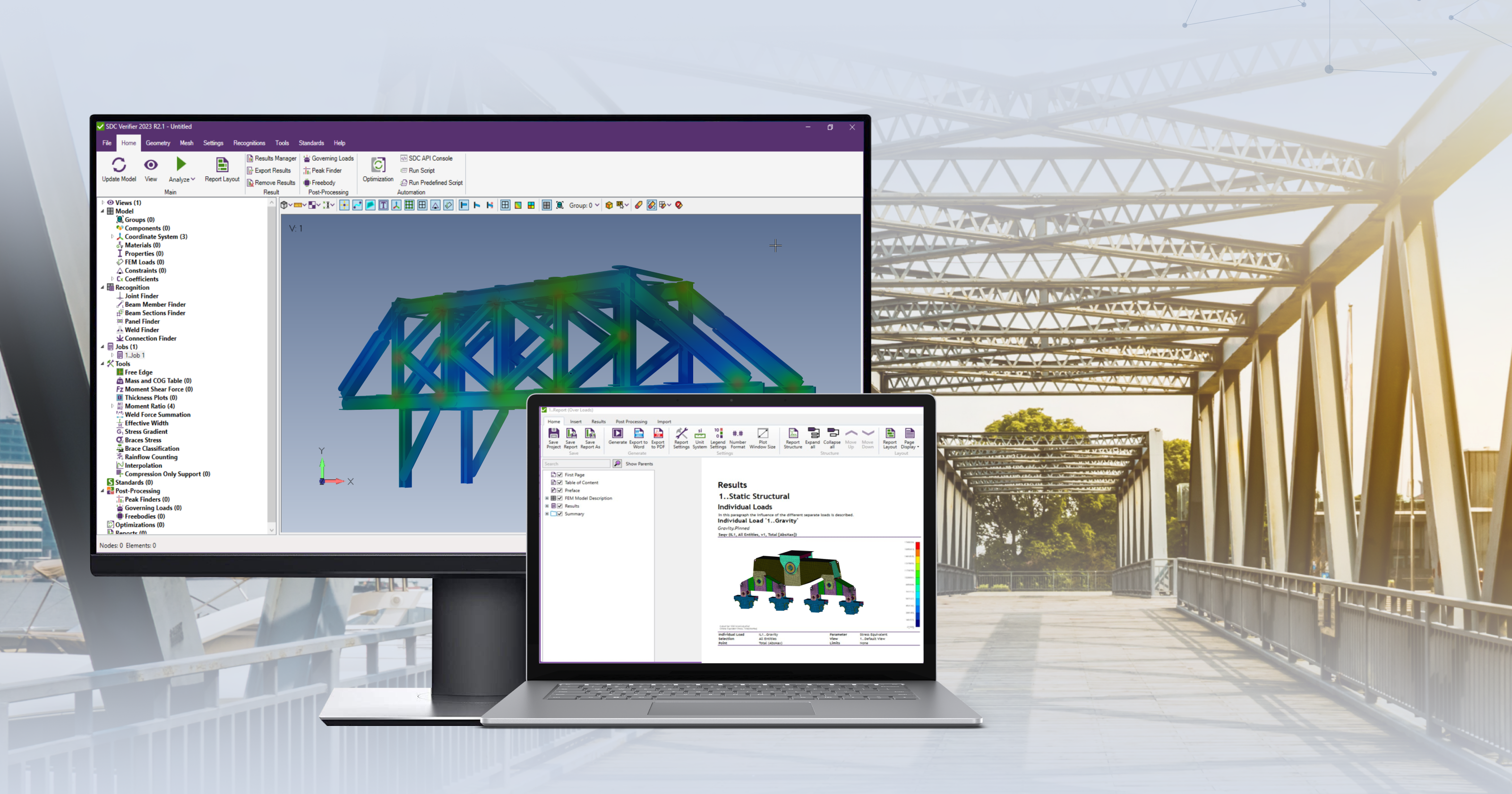
The safety and stability of civil structures are paramount in civil engineering. Failure to address design risks can lead to catastrophic consequences, endangering lives and causing substantial economic losses. The bedrock of civil infrastructure, including bridges, buildings, and other vital structures, relies on the robustness of design principles to withstand both natural and human-induced challenges.
Proactively identifying and addressing potential failure modes such as yielding, buckling, and fatigue is crucial in ensuring the safety, durability, and reliability of these structures. These failure modes represent significant vulnerabilities that, if overlooked, can undermine the structural integrity of civil structures.
Read our article on how engineers can bolster these structures by pinpointing potential issues, gaining a comprehensive understanding of them, and implementing targeted mitigation strategies.
Grasping the Structural Design Risks
The standard failure modes typically encountered in civil engineering are yielding, buckling, and fatigue.
Buckling is a sudden deformation that can lead to catastrophic collapse under compressive loads. This represents a significant risk with potential implications for public safety and operational continuity. Fatigue is a material failure mode caused by the initiation and propagation of a crack under cyclic loading. Yielding, prevalent in materials subjected to high loads, introduces the risk of plastic deformation, compromising structural integrity.
The consequences of these failure modes are extensive. By employing rigorous analysis techniques and proactive risk management strategies, engineers can ensure the structural integrity and resilience of civil infrastructure.
Understanding these risks is the first step towards designing safer and more reliable civil structures.
Adherence to Standards and Their Application in Structures Design
Industry standards and regulatory requirements, which consider factors such as material specifications, design methodologies, and performance criteria, are tailored to address the unique challenges of different structural components in civil engineering.
Adherence to established standards like Eurocode3, AISC, AIJ, AS, FEM, FKM, VDI is crucial. These standards cover various checks for members, including beam and plate buckling, connections, rivets, bolts, pins, weld capacity, strength, fatigue, fire design, and more.
Compliance signifies the application of best practices and regulatory guidelines governing civil engineering design and analysis.
The most common civil structures and their typical components include:
- Bridges: Beam bridges, truss bridges, arch bridges, and suspension bridges composed of I-beams, truss members, arch ribs, cables, and towers.
- High-rise Buildings: Skyscrapers and tall structures that require steel framing, including columns, beams, and braces.
- Industrial Facilities: Warehouses, factories, and manufacturing plants based on steel frames, roof trusses, wall panels, staircases, and walkways.
- Stadiums and Arenas: Large-scale structures designed to accommodate crowds and withstand heavy loads, with components like steel roof trusses, supports, precast steel risers, beams, panels, and columns.
- Airports: Terminal buildings, hangars, air traffic control towers, and aircraft maintenance facilities, including pipelines, cables, conduits, distribution networks, conveyor belts, hydraulic systems, subgrade, and drainage systems.
- Railway Stations: Platforms, canopies, railway bridges, and overhead structures along railway lines with bracings, trusses, foundations, and piers.
- Power Plants: Thermal, nuclear, and renewable energy facilities with boiler structures, turbine halls, cooling towers, chimneys or stacks, steam generators.
- Water Treatment Facilities: Structures such as water treatment plants and reservoirs with distribution pipelines, storage tanks, filtration systems, and chemical treatment units.
- Highways and Roads: Overpasses, guardrails, sign structures, retaining walls, and other components.
Each of these structures presents unique challenges and requirements, underscoring the importance of standards compliance in civil engineering.
The Integral Role of SDC Verifier in Civil Engineering
In the realm of civil engineering, precision and reliability are paramount in every structural design. This is where SDC Verifier steps in.
SDC Verifier is not just software; it’s a reliable assistant for engineers, designed to automate complex calculations. It helps mitigate structural design risks and ensures the safety and integrity by utilizing prebuilt standards used in the civil industry. Moreover, it offers the flexibility to implement any custom, local, or global standard.
* FEM 1.001 (3rd, 1998) (Rules For The Design of Hoisting Appliances), EN13001 Crane safety – General design (EN 13001, 2018), DIN 15018 (1984) (Cranes. Steel structures. Verification and analyses) are usually used as crane standards, but also are used in Civil structures verification, especially for industrial buildings that use lifting equipment.
Simulation Capabilities
SDC Verifier employs advanced simulation and verification technologies to automatically assess structural performance under various loading conditions, identify potential failure modes, and optimize designs for maximum efficiency and reliability.
It works on top of popular modeling environments and also serves as an independent FEA and design modeling solution based on the NASTRAN solver.
By integrating simulation and analysis tools into a user-friendly platform, it enhances workflow efficiency and reduces the likelihood of errors arising from data transfer and interpretation within multiple tools.
Recognition Tools
Despite the model consisting of multiple different finite elements, SDC Verifier aids users in automatically detecting the necessary components for various checks, such as beams/columns for beam buckling checks, joints and connections for connection checks, plate fields for plate buckling checks, welds for fatigue and weld capacity checks, and bolts for bolt checks.
Design Codes Checks
Following the detection phase, the full procedure prescribed by the standards (e.g., Eurocode 3, AISC, etc.) is integrated.
All formulas are automatically computed and checked against the requirements of the standard, allowing users to directly see all compliance issues and successful results.
SDC Verifier guarantees compliance with industry standards and regulatory guidelines, making it an essential tool for risk minimization.
Reports Generation and Optimization
All the aforementioned steps are automatically documented with the help of the reporting tool.
Essentially, all information visible in the software, whether it’s a model description item, calculation setup, or results, can be easily added to the report. For typical project ideas, a standard template can be created, saving a significant amount of time.
If a structural design is not optimal, SDC Verifier automatically optimizes it as many times as needed to achieve the highest possible effectiveness level.
By incorporating the latest rules and requirements, SDC Verifier enables engineers to validate designs with precision and certainty, mitigating the risk of non-compliance and ensuring adherence to best practices.
Conclusion
By automating Finite Element Analysis (FEA) and complex calculations, ensuring compliance with industry standards, and facilitating an efficient workflow, SDC Verifier streamlines the design process and enhances structural performance.
Explore the capabilities of SDC Verifier and harness its power to implement effective risk mitigation strategies in your projects. With SDC Verifier, you’re not just designing structures; you’re shaping the future of civil engineering.